Choosing the Right Feedback Device: Why the Smart Multi-Turn Feedback Device Stands Out

Wednesday, April 9, 2025, 11:00 a.m. ET
Position feedback devices are vital for servo motor precision. Our webinar explores top technologies, guides you in selection, and introduces SFD-M, a smart, high-performance feedback device ideal for modern servo systems.
Optimizing Industrial Communication: Using Fieldbus Technology
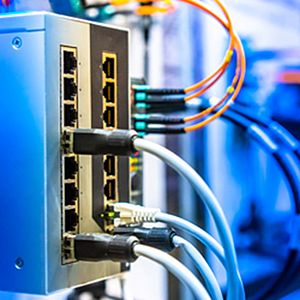
Thursday, April 10, 2025, 11:00 a.m. ET
Streamline communication in industrial operations using the optimum fieldbus technology. Learn the basics, explore Kollmorgen product solutions for seamless fieldbus integration, and understand the options and advantages offered by several industry-standard fieldbus solutions.
AKD2G Quick Setup Guide
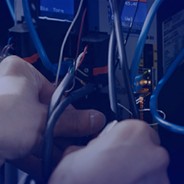
Wednesday, April 16, 2025, 11:00 a.m. ET
Learn how to use AKD2G Workbench software to set up your drive to perform next-generation motion tasks—quickly, confidently, productively.
Advanced Configuration for the AKD2G Dual Axis
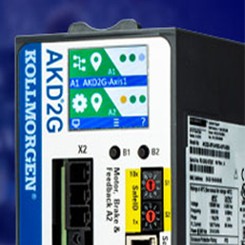
Thursday, April 17, 2025, 11:00 a.m. ET
Take full advantage of the dual-axis drive capabilities. Learn how to control two axes with one drive, including triggering inputs, tuning, troubleshooting and data capture.
Selecting a Frameless Servo Motor
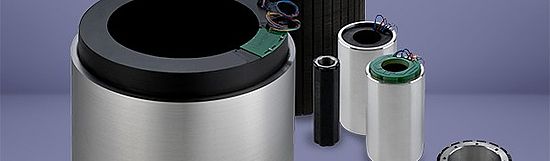
When you need exceptionally compact, precise, environmentally resilient motion, consider the advantages of a frameless motor. Based on your application, this interactive tool helps you decide: Housed or frameless — and if frameless, which model?
The Key to Next-Generation Surgical Robots
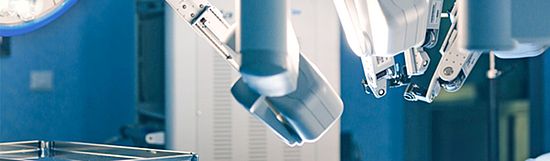
Surgeons want robotic cameras and instruments to operate as closely together as possible for an accurate field of view and minimal patient trauma. Learn how next-generation frameless motors are advancing the state of the art for high-performance, high-precision robots
Accelerate Your Design Processes with Kollmorgen

Take advantage of Kollmorgen's 3D CAD library to optimize design accuracy. Access 50,000+ configurable motion product models and easily integrate them into your engineering projects.
Incorporating Frameless Motors Into an Environmentally Resilient Design

High radiation, high vacuum, deep-ocean pressures, hazardous atmospheres and more — all of these environments call for specialized engineering to ensure reliable long-term performance. Learn why and how to embed frameless motors in the most compact and resilient possible design.
Keep Your Field Robot on the Job Longer, Working Stronger

Robot-ready motors designed for optimum size, weight and efficiency in specialized applications can extend your field robot’s operating time, range and reliability. Learn how to engineer greater success for the robots that perform difficult jobs while keeping humans safe.
Monitoring and Controlling Brakes Through On-Drive
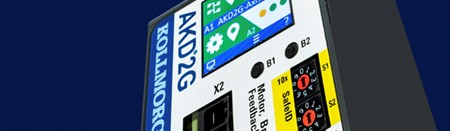
Functional Safety Technology
Without proper brake monitoring and testing, vertical loads can be hazardous. However, ISO 13849-1 does not allow brake testing functions to be embedded into standard machine controls. Learn the simple way to comply while achieving the safety level you need.
Clean Mirrors for Clean Energy
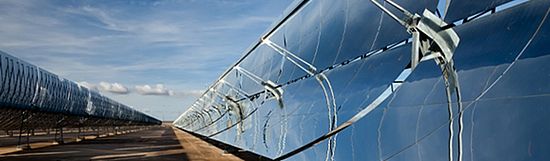
To keep energy flowing, heliostat solar plants need to keep thousands of massive mirrors clean. Learn how Kollmorgen motion helps increase maintenance efficiency by 500% and cleaning efficiency by 2,400% while operating in unpredictable terrain at temperatures often below –30ºC.
AKMA: Durable, Cleanable, Versatile, Built to Perform
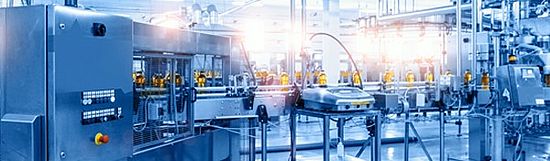
For applications exposed to medium or heavy washdowns, you need motors specially designed to reduce the risk of water ingress — and one that will meet your specific requirements. Our full line of AKMA motors deliver durability, cleanability and versatility, plus top servo performance day after day, year after year.
How to Use Motioneering to Size Your Application

Wednesday, March 12, 2025, 11:00 a.m. ET
If you’ve ever struggled to choose products with the best fit and performance for your application—or if you’ve never sized an application before—this session is for you. We’ll take you step-by-step through the process using the industry’s simplest, most powerful sizing tool.
Save My Seat
Creating Advanced Motion Profiles

Thursday, March 13, 2025, 11:00 a.m. ET
Size products and create complex motion profiles for additional mechanism types, such as conveyor systems and electric cylinders. This session will teach you best practices you can apply to any motion project.
Save My Seat
How to Set Servo Motor Phasing for Effective Axis Control
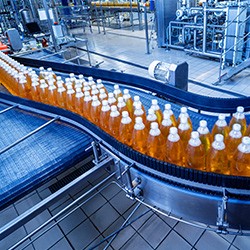
Wednesday, March 19, 2025, 11:00 a.m. ET
Electronic commutation in a brushless servo system depends on feedback data as well as correct phasing between motor and drive. But phasing can be altered under circumstances that are often misunderstood. In this webinar, we’ll show you how to get it right for optimum control.
Save My Seat
Incorporating a Direct Drive Linear Motor into Your Machine Design
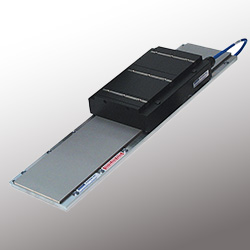
Thursday, March 20, 2025 11:00 a.m. ET
Conventional rotary-to-linear motion systems are limited by physics. Direct drive linear motors, with fewer components and no mechanical coupling, break through these restrictions to deliver exceptional accuracy, durability, and speed. Attend this webinar to explore how you can transform your next machine design.
Save My Seat
The No-Compromise Motor: TBM2G
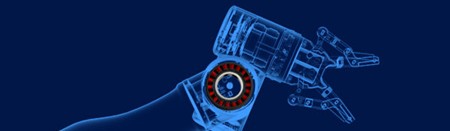
Get the highest torque density, at the speeds you require, in a robot-optimized form factor, with minimal temperature rise. TBM2G means no more tradeoffs.
8 Tips to Reduce or Eliminate EMI Noise
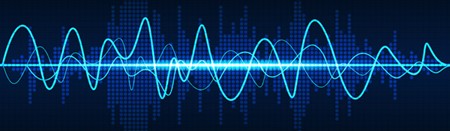
Electromagnetic interference can wreak havoc with sensitive electronics, compromising the safety and reliability of your machine. Avoid unplanned downtime, loss of productivity or even hazardous operating conditions by implementing these 8 simple yet essential techniques.
Advancing the State of the Art for Surgical Robots
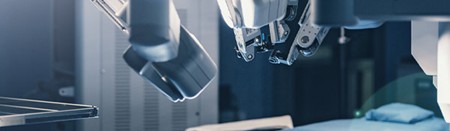
Next-generation surgical robots offer the ability for multiple instruments to approach the surgery site at practically any angle, including nearly parallel. Learn how you can minimize axial joint length to bring surgical arms as close together as possible.
Motors for Missiles: Optimizing Performance
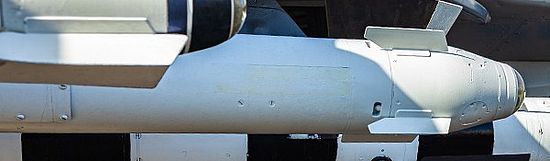
In defense applications, failure is not an option. Missile guidance and control systems must perform flawlessly in the most extreme conditions of shock, vibration and temperature. Learn how to specify motion systems that keep sophisticated weapons reliably on target, from engineering concept to deployment.
Learn How Simple Perfect-Fit Motion Can Be
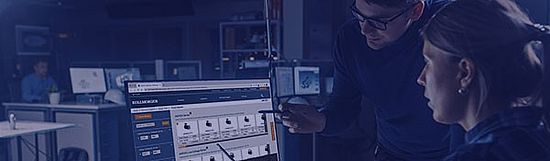
There’s no need to search through websites or catalogs looking for a perfect fit. Our online Product Selector tool does the research for you. Simply enter the torque, speed, power, size, and other requirements and be guided to motors, drives and cables that best suit your application.
Smart Technologies for Food Packaging Performance
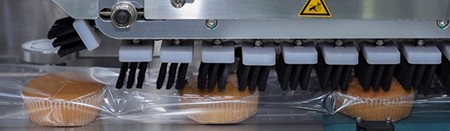
Today’s food packagers are looking for machines that are more compact and automated, driving greater throughput and accuracy. However, it can be challenging to achieve these goals using individual components that were designed with little regard for integration. Learn a smarter approach — building machines with much of the integration built in at the component level.
Space-Worthy Motors to Meet Any Mission
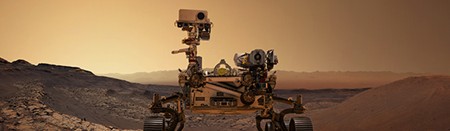
The shock and vibration of launch. The extremes of vacuum, temperature and radiation. Missions that last for many years. Crews that depend on absolute system reliability. Learn how Kollmorgen meets all these challenges with motors specially designed for the rigors of space.
What is a Frameless Motor?
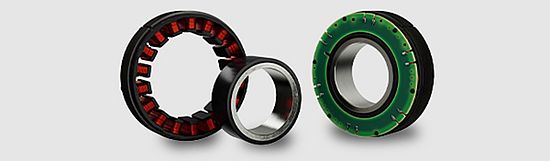
Curious about frameless servo motors, how they operate, and how they differ from other motor technologies? Or knowing when a frameless motor is the best choice for your application and what key features to look for? Kollmorgen can help..
Size Your Motor and Drive in Minutes
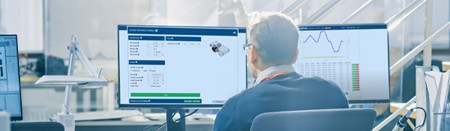
Save engineering time and eliminate uncertainty. Motioneering is the guided selection tool that shows you optimum motor and drive choices based on the application requirements you enter. Solve selection and sizing challenges in minutes, automatically.
Motion Technology in the Service of Corporate Values
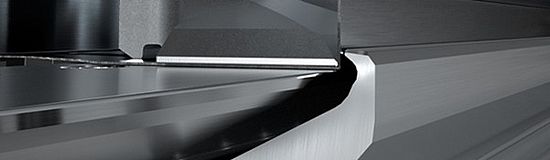
When Salvagnini, a major global manufacturer of sheet-metal processing equipment, wanted to improve energy efficiency and productivity, it turned to Kollmorgen for advanced motion technology and expertise. Learn the solution and the results.
Greater Scan Safety and Comfort for Every Patient
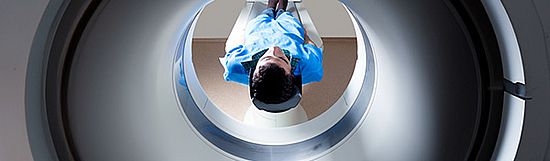
Read and learn how motion systems can be engineered to reduce radiation exposure, audible noise and scan time. Patients deserve a better experience, and Kollmorgen can help you provide it.
Powering a Submersible Robot for In-Service Inspection of Fuel Storage Tanks
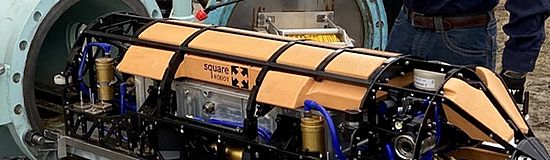
Why drain a massive fuel tank so that humans can enter and inspect it, when an innovative submersible robot can do it more efficiently, more cost effectively, while keeping people and the environment safe? Learn how Square Robot used highly modified frameless motors from Kollmorgen to help make this extraordinary new technology possible.
SafeMotion™ Monitor Upgrade Offers Greater Design Flexibility
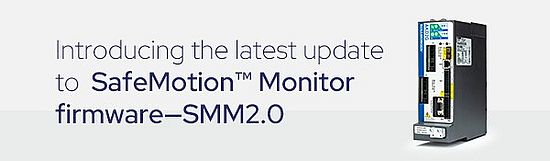
Kollmorgen announces the latest update to its SafeMotion™ Monitor (SMM) firmware: SMM2.0. This upgrade allows OEMs to use SMM functional safety features with a larger range of HIPERFACE-DSL encoders and motors, supporting a wider range of high-performance applications.
All About Functional Safety
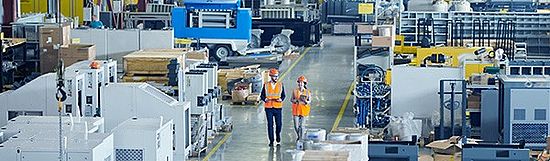
Functional safety is becoming a necessity in a variety of industries. But what are the specific considerations? How will designers navigate them? And how can those who are less familiar with functional safety principles get up to speed?
Intentional Design. Streamlined Setup. Ultimate Performance.
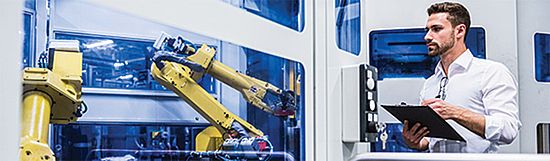
The Kollmorgen 2G Motion System offers engineers the best of both worlds: A servo motor and drive system designed to work together for ultimate compatibility, ease of setup and higher performance; and the flexibility, power and control to bring any design to life—with individual components as needed.
Achieving Ultimate Motion Precision Using Frameless Servo Motors
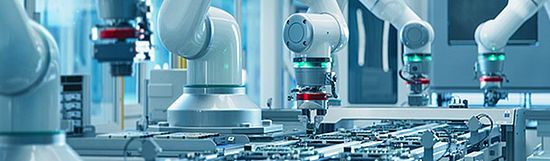
Frameless servo motors offer ultimate precision and torque in the most compact form factor while enabling effective protection from environmental extremes. Learn how to successfully incorporate a frameless motor into your application.
Optimizing Motion for Electro-Optical/Infrared Imaging
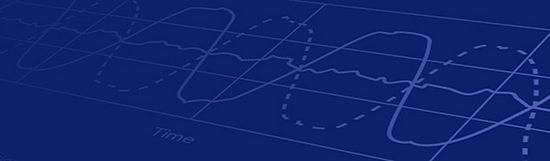
Many applications require very high torque and smooth motion at relatively low motor speeds, especially EO/IR. This blog will lay out the concepts surrounding cogging torque and torque ripple to help you determine what technology will support your application the best.
5 Critical Insights: Interpreting the Bode Plot

Bode plots reveal the unique frequency-response fingerprint of servo mechanisms. But how can you read the fingerprint and use it to fine-tune your system? Optimize machine motion by unlocking these five key Bode plot insights—complete with illustrated examples.
Adjusting Standard Motion Profiles to Optimize Operating Speed and Time On Demand
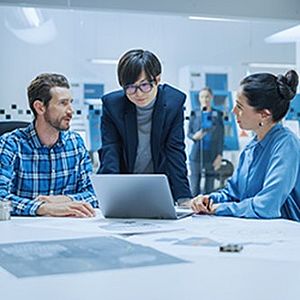
The most commonly used motion profiles don’t always provide optimum results. Learn simple adjustments you can make to achieve the ideal speed and move time for your application — without the need for guesswork or extensive trial and error.
Mastering Dynamic Motion

Revolutionizing Exoskeletons On Demand
New innovations in exoskeleton design promise to bring transformative possibilities to military, logistics, healthcare and other applications. Learn how to navigate the unique mobility challenges involved, maximize motor efficiency, and ensure that your motion solution is highly manufacturable and scalable for marketplace success.
Maximize Missile Performance with Advanced Frameless Motors On Demand
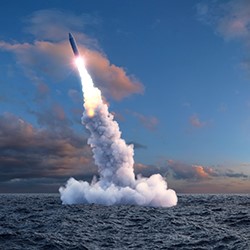
Missile manufacturers are under pressure to design and produce ever more sophisticated systems in greater quantities. Learn how to optimize missile guidance and control systems with a solid understanding of the frameless motor design principles that make a difference for actuator size, weight, performance and reliability. Join this informative online training.
How to Set Servo Motor Phasing for Effective Axis Control On Demand
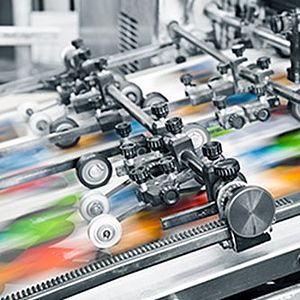
Instead of mechanical commutation, brushless servo motors rely on electronic commutation based on feedback data and motor phasing. Join this online session to learn how to establish the correct phasing between motor and drive for optimum servo control.
Watch Now
Motor Windings
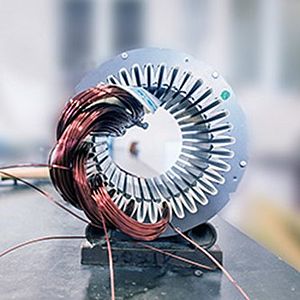
Understand How They Work and Affect Performance On Demand
To maximize your application’s motion performance, specify the optimum servo motor. Stator windings play a major role in determining motor torque, velocity and horsepower. Join us online to enhance your engineering skills through an in-depth knowledge of motor windings.
Master Servo Motor Parameters
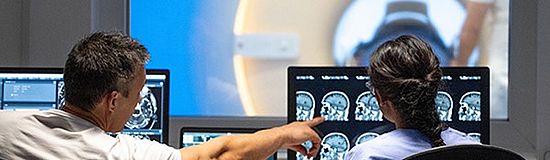
With no industry-standard way of publishing servo motor parameters, you run the risk of motor/drive mismatches that significantly affect performance. Our latest white paper provides expert insights and practical solutions to help you apply parameters correctly, avoiding design and manufacturing setbacks.
Kollmorgen and Stereotaxis Advance the Precision and Safety of Surgical Robots
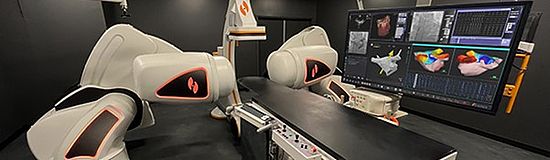
The new Genesis surgical robot is revolutionizing cardiac ablation procedures, giving patients the promise of longer, healthier lives. Learn how Kollmorgen technology and expertise made the difference for a visionary surgical robotics company.
Stepper or Servo Motor? Here’s how to decide.
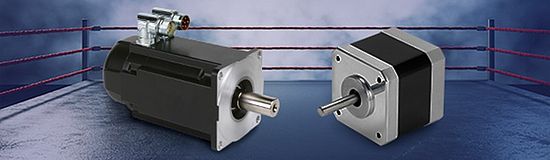
Stepper and servo systems each have advantages based on their differing design and operating principles. Understanding these differences is the key to choosing the best technology for your application. Check out our Blog in Motion for an overview of the most common selection scenarios.
Selecting a Frameless Servo Motor
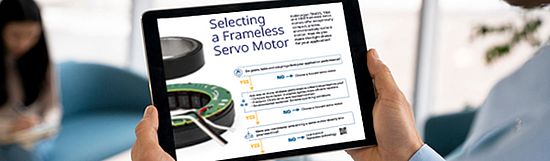
Our interactive online tool steps you through the design questions and answers you need to choose between a housed or a frameless motor. And if frameless is the right choice, it guides you to the model that best fits your application. Simplify your selection.
Build a Better Humanoid Robot
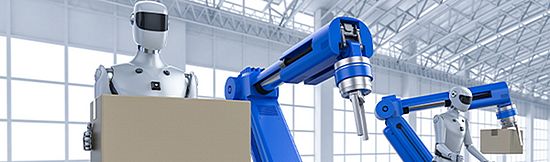
Humanoid robots must be capable of highly dynamic motion, coordinated across dozens of robotic joints, in order to manipulate objects of varying size and weight while simultaneously carrying their own weight and navigating unpredictable environments. The motion requirements are extremely complex compared to conventional industrial robots. Learn how to understand and solve them.
Minimize Weight and Size to Maximize Efficiency

By specifying lighter, more compact, higher-efficiency motors, you can achieve optimum performance for positioning UAV flight-control surfaces, visualization systems, sensors, payloads and more. Learn how to design a more capable aircraft, bring it to market faster, and support it confidently throughout its lifecycle.
Frameless Motors for Propulsion Systems and Extreme Environments

When a housed motor can’t provide the environmental resilience you need in the compact form factor you want, consider embedding a frameless motor into your mechanical design. Gain full control to resist deep ocean pressures, daily washdowns, high vacuum, ionizing radiation and other extreme conditions.
From Theory to Action

The Impact of Motor Science on Robotic Excellence
Thursday, November 21, 2024, 11:00 a.m. ET
Gain new technical insights into motor design for improved thermal dynamics and efficiency in robotic systems. Discover how to design high-performance motion solutions that optimize size, weight and cost while meeting the demand for higher payloads and faster operations.
Enabling New Surgical Possibilities
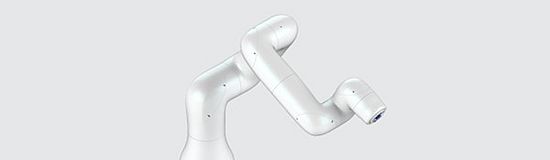
High-torque, low-temperature, compact-size motors are the key to a game-changing surgical robot design. Learn how advanced motion is improving patient outcomes and quality of life.
Improve Performance Without Redesigning Your Machine
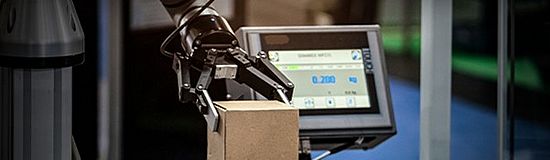
How can you improve machine performance while minimizing risks, costs and speeding time to market? Assess your options, from replacing individual motion components to a partial or complete redesign of your machine. Depending on your goals, the optimum strategy may surprise you.
Motion and Automation to Build a Better World
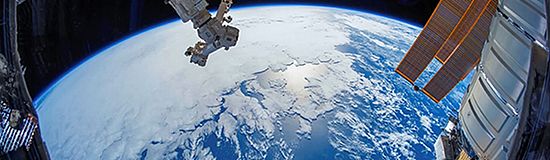
We’re helping engineers like you change warehouse efficiency, factory productivity, healthcare delivery, mobile robot and automated vehicle capabilities, space journeys and more. It’s all about more ambitious, capable and confident motion. Get inspired for your next project with Kollmorgen.
Your Agricultural Robot Can Be More Productive
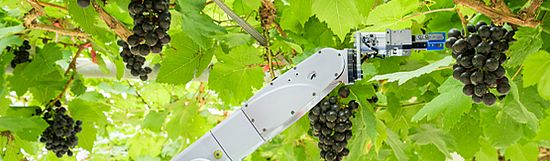
Farm costs are rising. Labor is in short supply. Margins are slim. That’s why farmers are looking for robots that can help significantly improve speed and yield. Learn the role that advanced motion can play to help grow a stronger agricultural business.
Easy-to-Clean, Durable Motion Systems for Food Processing and Packaging
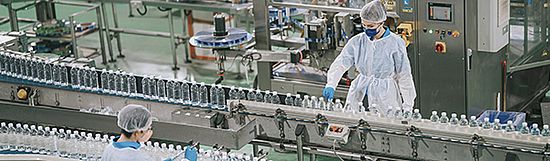
Food safety is a must, yet the need to wash down production and packaging equipment brings many risks. High-pressure spray and chemicals can damage motors and other components. Cleaning crews may take shortcuts. Pathogens may remain despite best efforts. Learn how to solve all of these issues in a cleaner, more productive machine.
Optimize Form and Fit with Our 3D CAD Product Models
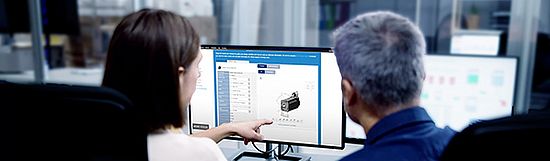
Search, configure and visualize more than 50,000 motion product models on demand. Then download 3D models in CAD for direct incorporation into your design.
Direct Drive Technology Enhances Accuracy and Throughput for EV Battery Production
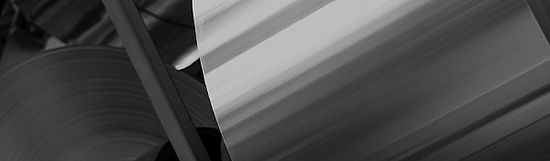
Electric vehicles are changing the world for the better. But with their rapid adoption, lithium-ion battery manufacturers need to maximize production quality and speed. The electrode coating process is crucial, requiring utmost precision. Learn how direct drive technology is bringing extraordinary new possibilities to the industry.
Greater Scan Safety and Comfort for Every Patient
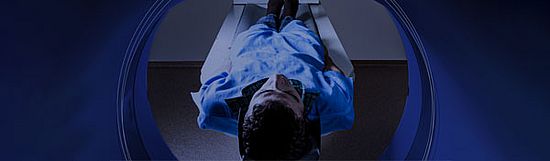
Read and learn how motion systems can be engineered to reduce radiation exposure, audible noise and scan time. Patients deserve a better experience, and Kollmorgen can help you provide it.
Electric Motors for Missiles: Optimizing Performance
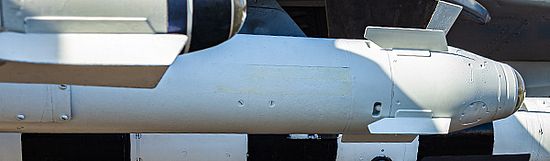
In defense applications, failure is not an option. Missile guidance and control systems must perform flawlessly in the most extreme conditions of shock, vibration and temperature. Learn how to specify motion systems that keep sophisticated weapons reliably on target, from engineering concept to deployment.
Increase machine performance with powerful, highly scalable control
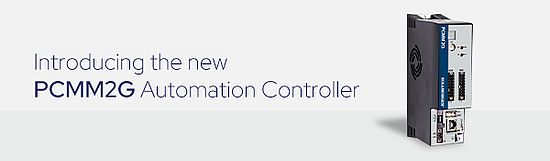
Thursday, October 17, 2024, 11:00 a.m. ET
Register for the live session or to receive a link to the recording
Discover the next generation of motion control. Our new PCMM2G controller offers significantly higher performance, scalability from 1 to 64 axes of motion, and simple integration in a compact package. Join us for a revealing online tour.
MAC231-P IP67/69K Stainless Steel Integrated DC Servo Motor for Harsh Environment JVL

MAC231 motor - with a new generation encoder with unlimited downtime, no battery required!
JVL is proud to announce the brand new generation of our IP67 320W RMS, S3 25% duty cycle servo motor. Protected against high pressure and high temperatures, this new engine is based on previous designs and customer feedback collected over many years, and offers a wide variety of options and options that make this product suitable for almost any application.
Key Features:
IP69K optional
Highly dynamic servo controller
Industrial Ethernet - 6 protocols
Absolute multi-turn encoder with unlimited downtime (no battery!)
Recommended supply voltage 48 VDC
1 kW Top performance
Position accuracy ±0.4° (±9.1 pulses) thanks to the magnetic encoder
Optional built-in gearbox for torque up to 50 Nm.
Protection class up to IP67
A wide program of optional modules
Connectors: industrial M12
Built-in ePLC PLC
What's new?
Absolute multi-turn encoder based on collection technology without battery or device
High performance Ethernet similar to larger MAC engines
New MOSFET technology for higher efficiency and cooler motor
Encoder resolution 8192 CPR (higher resolutions planned)
Options:
STO and/or brake connector
More advanced FOC filter for lower noise and better engine performance
100% stainless steel shaft, flange, tube and rear end cap.
Special Teflon seal for long-term waterproof operation.
Cost effective in harsh wet corrosive environments
A shaft seal and leak-proof cable glands provide a watertight seal at both ends.
Ideal for food, liquid, pharmaceutical, washing, chemical, bakery and beverage machinery, etc.
Option for a built-in planetary gearbox.
Option for embedded PLC, RS232/485, Profibus, CANbus or industrial Ethernet (EtherCAT, EtherNet/IP, Profinet, Modbus TCP, Sercos III and others)
Efficient and Effective Risk Management for Vertical Axes
With new safety standards that require periodic brake testing and prohibit embedding of test functions within standard controls, what’s the best way to keep operators safe, maximize productivity, and simplify machine design? Learn the advantages of on-drive safety functions.
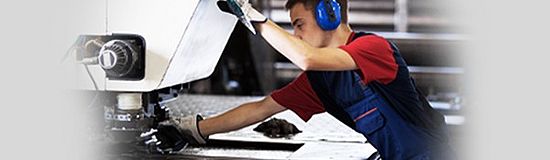
Motors Designed for the Rigors of Space
With tens of thousands of new satellites in the planning, the rush is on to utilize low Earth orbit. Learn how motors designed for the rigors of space and the realities of the marketplace will be key to winning the new space race.

Online, Interactive Product Selectors
From torque, speed and power to form factor, controls and accessories—the perfect fit is key to your application’s success. Use our selection tools to choose motion products with confidence. Our instructional video shows you how simple it can be.
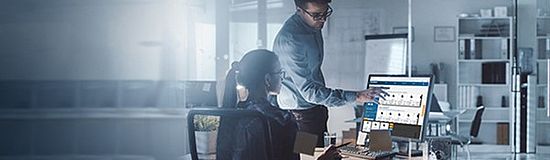
Kollmorgen Announces the New PCMM2G Motion Controller
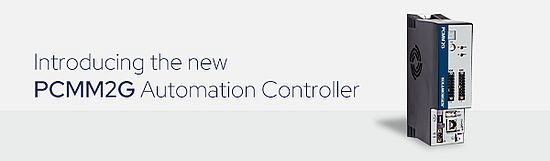
For simple machines or complex automation environments with up to 64 axes of synchronized motion, Kollmorgen’s new PCMM2G controller introduces next-generation performance and flexibility. It’s simple to use and integrates seamlessly with virtually any system.
PCMM2G: Next-Generation Performance in a Powerful, Compact Controller
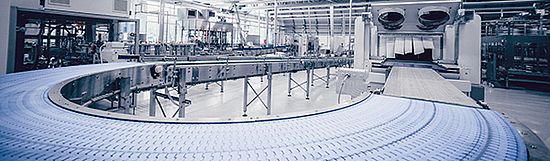
Take control. The new PCMM2G automation controller is the simple way to gain greater flexibility, speed and ease of use. It seamlessly integrates with Kollmorgen Automation Suite and even supports third-party devices, providing up to 64 axes of synchronized motion.
Introducing the Next-Gen Motion Controller
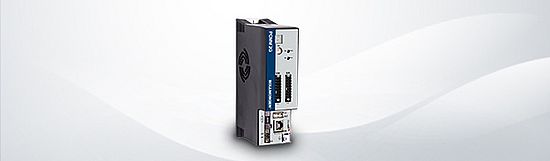
Increase machine performance with powerful, highly scalable control
Thursday, October 17, 2024, 11:00 a.m. ET
The new PCMM2G delivers 1.5–3.5 times the performance of previous motion controllers, with scalability to control 1–64 axes of motion. It’s easy to integrate with practically any automation system. Learn more in this online demonstration.
How to Set Servo Motor Phasing for Effective Axis Control Thursday
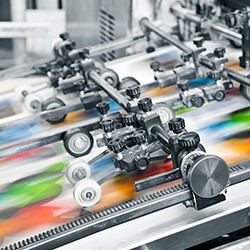
October 24, 2024, 11:00 a.m. ET
Instead of mechanical commutation, brushless servo motors rely on electronic commutation based on feedback data and motor phasing. Join this online session to learn how to establish the correct phasing between motor and drive for optimum servo control.
How to Set Up Your AKD for Success
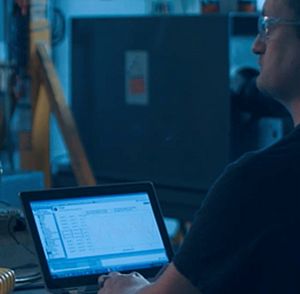
October 23, 2024, 11:00 a.m. ET
New to setting up a servo drive? Already experienced but looking for tips for a more effective setup process? This session is for you! Follow along and learn how to minimize setup time, apply best practices, and create precise motion—step by step.
Save My Seat:
Advanced Motion with AKD Thursday
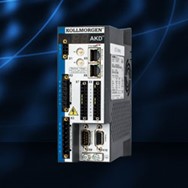
October 24, 2024, 11:00 a.m. ET
Create intricate motion tasks, identify mechanical compliance, and increase performance by mastering the programming and diagnostic tools built into the AKD.
Save My Seat:
Compact Joint Design for the Next Generation of Surgical Robots
In robot-assisted procedures, surgeons value the ability to place multiple instruments in a nearly parallel orientation. Learn how to design compact robotic arm joints that give surgeons the dexterity they need and help improve patient outcomes.
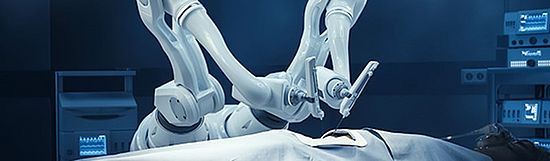
Frameless Motor Performance Curve Generator
Map speed-torque curves based on variables including current, voltage, ambient temperature and winding factors. It’s easy to specify the optimum frameless motor for your application using the online Performance Curve Generator.
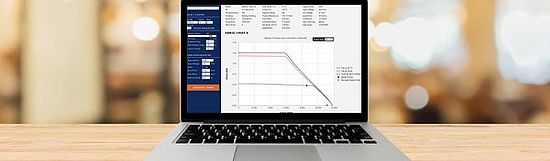
Exceptional Motor Performance for Superior Robots
When designing a collaborative robot, you want each joint to deliver optimum torque density and smoothness while keeping size and weight to a minimum. That’s why we designed a new generation of robot-ready frameless motors.
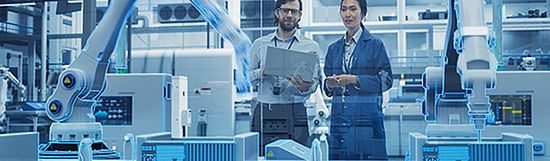
Discover Smarter Packaging Technologies
How can you make your form, fill and seal machine simpler to use and more compact? How can you streamline programming, operation and maintenance? How can you enhance throughput, quality and safety? Read our latest blog to learn about the state of the art in motion for packaging.
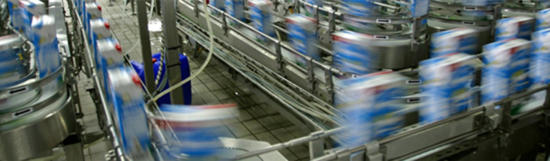
Deliver High Performance in a Compact Form with TBM2G Frameless Motors
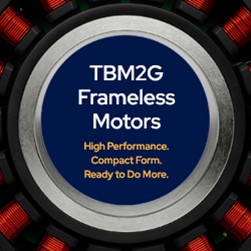
With significantly higher torque density in a more compact axial design, next-generation TBM2G frameless motors are ready to perform, ready to fit your design, and ready to scale. Learn how you can engineer a more capable machine, without compromise.
Get Higher Performance in Less Space with AKM2G Servo Motors
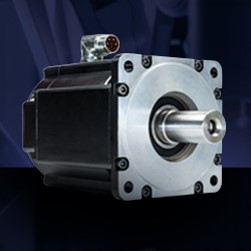
Next-generation AKM2G servo motors provide substantial performance improvement without changing the motor mounting or consuming more machine space. And they’re available with a wide range of options including extensive feedback, shaft, connector and support for functional safety.
Experience and Expertise for Defense and Aerospace
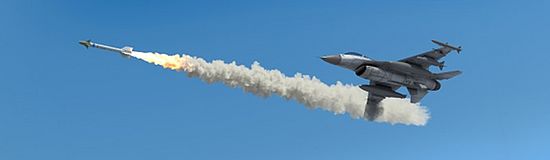
In the defense industry, program specifications, contractual obligations and provisioning requirements are far more demanding than most civilian applications. With more than 70 years of serving customers in this industry, Kollmorgen is up to the challenges.
5 Motion Tips for High-Definition Metal Cutting Performance
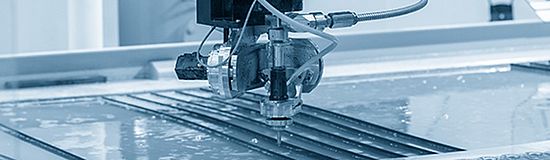
The success of your metal-cutting machine depends on the performance of its motion systems. Learn how to optimize the fieldbus architecture, control loop bandwidth, servo motor design, feedback system and cabling to achieve superior cutting quality and speed.
Direct Drive Helps Improve the Production Speed and Qualityof Electric Vehicle Batteries

The demand for electric vehicles is soaring. Learn how a major manufacturer of lithium-ion blade battery production equipment significantly increased throughput and quality using direct drive technology to improve its competitive position.
Stop, Hold and Go Safely: Motion Tuning for Vertical Loads
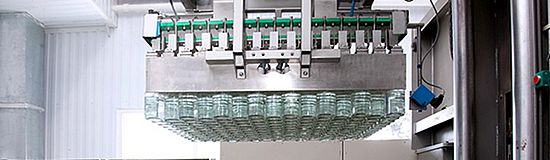
Vertical loads need to be properly managed to avoid the potential for wasted product, operational interruptions or even human injury. Learn best practices for configuring your servo drive’s vertical load handling, including Safe Brake Control and Safe Brake Test functions.
Increase Your Machine’s Accuracy and Reliability with Secondary Feedback
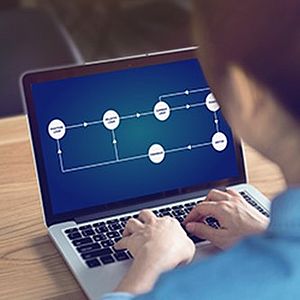
Thursday, September 12, 2024, 11:00 a.m. ET
Complex, high-speed motion axes can often benefit from a secondary feedback device located near the load in addition to standard servo motor feedback. Learn when and how to add secondary feedback for predictable performance under the most demanding conditions.
Save My Seat
The Foundations of Electric Motion
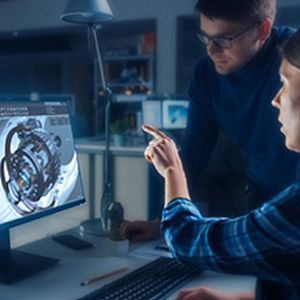
Thursday, September 19, 2024, 11:00 a.m. ET
Learn the details of different motor types, open vs. closed loop control systems, and how to configure the optimum motion system for each machine axis.
Save My Seat
The Foundations of Motor Performance
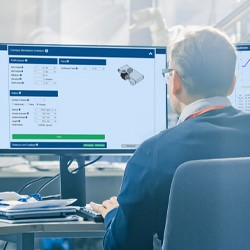
Friday, September 20, 2024, 11:00 a.m. ET
Join this session to gain the practical knowledge you need to optimize servo performance, including how to specify the right feedback device and resolution, achieve efficient and cost-effective inertia matching, and more.
Save My Seat
What is a Closed-loop System?
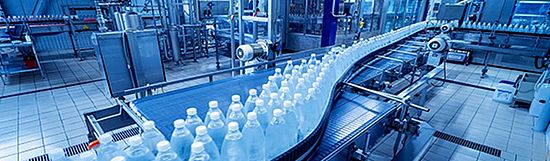
When you need the most precise control of torque, speed and/or position, servo motors and drives are likely your best choice. But how exactly does a servo system achieve such precision? Read this brief Q&A to learn the fundamentals of closed-loop control.
Explore the Possibilities of Frameless Servo Motors
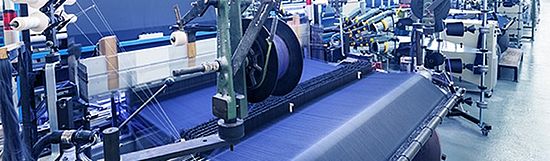
The Kollmorgen KBM series enable applications that are lighter, more compact, more precise and better protected from environmental extremes. Learn whether frameless motion is right for you — and how to choose your ideal motor configuration.
Frameless Motors for Gimbal Motion
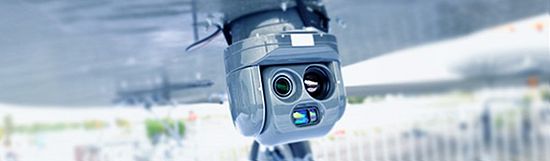
Multi-axis gimbals for imaging, sensing and communications systems benefit from compact, lightweight, ultraprecise motion. TBM2G frameless, direct-drive motors provide the ideal solution. Learn why and get technical advice for engineering the optimum gimbal design.
Motion Control System Selection in Next-Gen Robotics
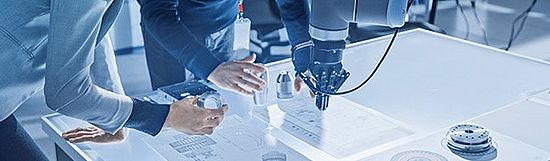
Tuesday, August 27, 2024, 2 p.m. ET
Yoshi Umeno, Global Industry Manager - Robotics - Kollmorgen
Greg Harnsberger, Senior Manager of Global Industry Marketing - Portescap
Unlock the full potential of your robotic designs in our upcoming webinar. We'll explore critical factors in motor selection, reveal how to achieve seamless communication with feedback devices, and examine real-world case studies of optimized motion control systems, from collaborative surgical robots to humanoids.
The Right Motor For Tough Conditions
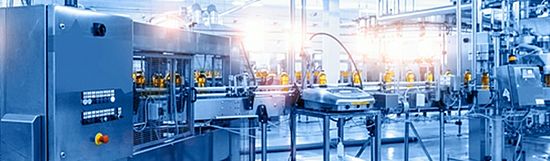
Whether you’re designing for tough medium or heavy washdown applications or all-weather conditions, AKMA motors offer the ideal feature set. See which AKMA motor meets your unique specifications with our streamlined product brochure.
eVTOL Motion, From Design to Delivery
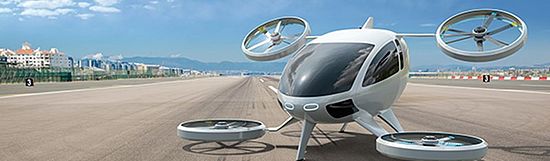
Did you ever imagine you could take an air taxi from the airport to a downtown location? Or see road congestion give way to direct, point-to-point delivery of goods overhead? With innovative eVTOL technology, all this and more could come true sooner than you thought. Learn how Kollmorgen is helping.
Increasing Trajectory Welding Speed in Lithium-Ion Battery Production
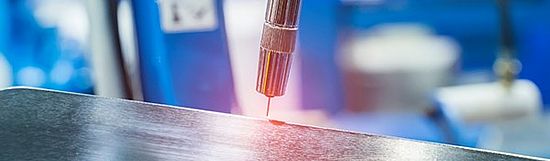
Electric vehicles and electronic devices are creating an exponentially growing demand for lithium-ion batteries. Learn how precise laser welding, controlled by Kollmorgen’s direct drive technology, improves control accuracy by 30% and boosts yield to over 99%, substantially improving the competitive position of electric vehicle battery manufacturers.
Exoskeleton Excellence: Greater Comfort, Safety & Mobility
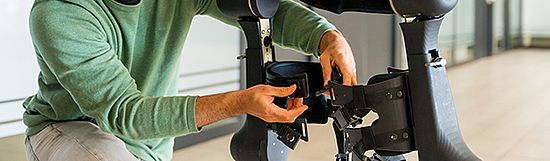
The exoskeleton market is at a tipping point. With an aging population, increases in chronic disease and no end in sight for serious labor shortages, exoskeletons offer tremendous potential. But how will engineers achieve the delicate balance of performance, safety and comfort?
Size Your Motor and Drive in Minutes
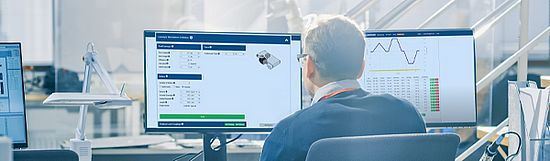
Save engineering time and eliminate uncertainty. Motioneering is the guided selection tool that shows you optimum motor and drive choices based on the application requirements you enter. Solve selection and sizing challenges in minutes, automatically.
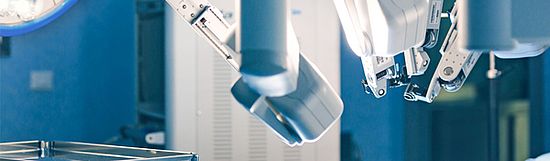
Surgeons want robotic cameras and instruments to operate as closely together as possible for an accurate field of view and minimal patient trauma. Learn how next-generation frameless motors are advancing the state of the art for high-performance, high-precision robots.
Essentials of Motion Control
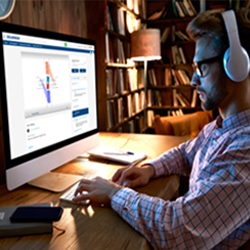
Register now and Learn at your convenience
The Essentials of Motion Control self-paced class, allows you to follow the path from electrical energy to physical motion, focusing on every opportunity to optimize motor efficiency and performance. Ready to get moving?
Get Started Now
Stepper Motor or Servo Motor: What are the key factors to consider?
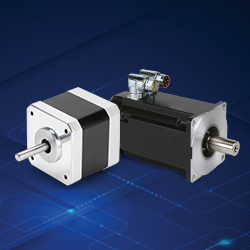
Stepper or servo? It’s one of the most common and important questions in motion engineering. And that’s why we’ve provided answers you can use in one of our most popular white papers ever. Read it, and make the right choice with confidence.
Get the White Paper
Three Design Considerations that Indicate a Machine Needs a Frameless Motor
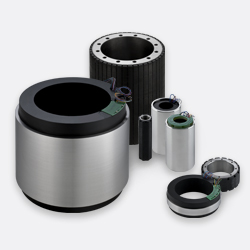
Does your machine need to operate in a smaller footprint, deliver enhanced performance or endure extreme conditions? Learn why a frameless direct-drive motor is likely your best solution.
Read the Blog
Still Designing to Decades-Old Inertia Matching Rules?
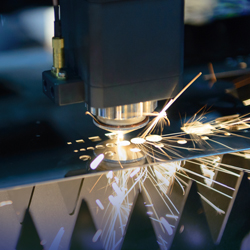
Machine Designers have pursued the idealized 1:1 inertia matching for the motor and load. But what if this rule no longer applied and you could use a significantly smaller motor and still achieve perfect motion? You can, and here’s how.
Get the White Paper
NEMA17 and 23 ball screw stepper actuator with piston rod drive up to 2200 N tip by JVL
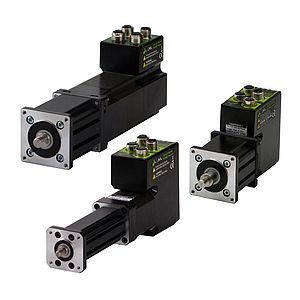
Introducing the latest innovation from JVL A/S, a global leader in integrated servo and stepper motors, the ServoStep™ range welcomes a ground-breaking addition: the Piston Captive Style Actuator, also known as the Electric Linear Rod Actuator. Designed with precision and durability in mind, this new drive boasts a built-in high-quality ball screw and non-rotating guide to ensure extended life. Unlike traditional setups, the ball screw is seamlessly integrated into the motor shaft, offering an exceptionally compact solution and shorter drive length.
Linear stepper motors can reduce costs and save space. No coupling, no additional bearing support and no assembly work required. It reduces not only costs and length, but also the failure rate due to fewer components and simpler construction. In applications with low radial load capacity, a linear guide is not required. The special design and use of a ball screw and low-friction guide allows for long life, increased efficiency or reduced maintenance requirements.
Functions:
- Stroke from 12.7 to 127 mm. (custom lengths available)
- Rolled ball screw 1, 2 or 4 mm/rev with C7 accuracy level
- Linear speeds up to 200 mm/s
- Accuracy 0.05 mm
- Non-rotating piston end
- Motor with double-row ball bearing for high axial load and minimum axial play
- Optional epoxy coating for IP65/67 coverage
- Rear brake option
- Ball linear bearing option for high radial loads
- Selection of precision leveler precision ball screws including C0 to C5
- Flexibility to select a customer-specific brand of ball screws
Various configurations are available
Discover unmatched performance and versatility in a variety of configurations. ServoStep™ drives are available in NEMA17 and NEMA23 sizes with plastic nuts with leads from 0.635 to 25.4 mm/rev and forces up to 2500 N. In addition, NEMA34 variants are offered with lead screw pitches from 2.54 to 25.4 mm and 2 or 5 mm/rev ball screw pitches that provide forces up to 4000 N. Alternatively, NEMA34 models are equipped with lead screws with plastic nuts and pitches from 2.54 mm to 25.4 mm that provide forces up to 3000 N.
Understanding Stepper Motor Winding Options: Series vs. Parallel
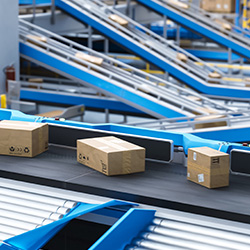
Thursday, August 15, 2024, 11:00 a.m. ET
Stepper motors can be wound in either a series or parallel configuration, and which style you choose can make a big difference for your application. Learn the nuances of stepper windings and how to make the best choice for different application scenarios.
Save My Seat
How to Use Motioneering to Size Your Application
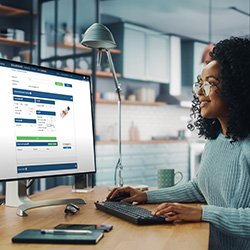
Wednesday, August 21, 2024, 11:00 a.m. ET
Calculating how servo system components will fit and perform in your application can be a challenge — unless you have the right tool for the job. Take a tour of Motioneering, and learn how to easily create basic motion profiles that can help you make the optimum choices.
Save My Seat
Creating Advanced Motion Profiles
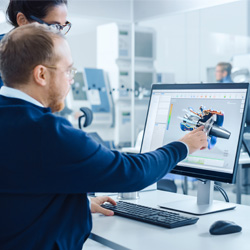
Thursday, August 22, 2024, 11:00 a.m. ET
Size products and create complex motion profiles for additional mechanism types, such as conveyor systems and electric cylinders. This session will teach you best practices you can apply to any motion project.
Save My Seat
Build a Better Humanoid Robot
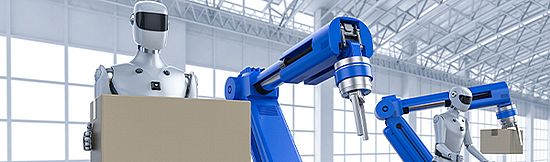
Humanoid robots must be capable of highly dynamic motion, coordinated across dozens of robotic joints, in order to manipulate objects of varying size and weight while simultaneously carrying their own weight and navigating unpredictable environments. The motion requirements are extremely complex compared to conventional industrial robots. Learn how to understand and solve them.
Minimize Weight and Size to Maximize Efficiency
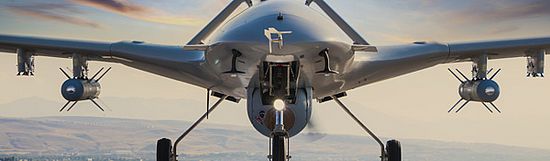
By specifying lighter, more compact, higher-efficiency motors, you can achieve optimum performance for positioning UAV flight-control surfaces, visualization systems, sensors, payloads and more. Learn how to design a more capable aircraft, bring it to market faster, and support it confidently throughout its lifecycle.
Frameless Motors for Propulsion Systems and Extreme Environments
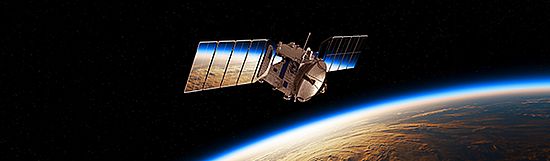
When a housed motor can’t provide the environmental resilience you need in the compact form factor you want, consider embedding a frameless motor into your mechanical design. Gain full control to resist deep ocean pressures, daily washdowns, high vacuum, ionizing radiation and other extreme conditions.
Cartridge DDR: Precise, Powerful, Simple
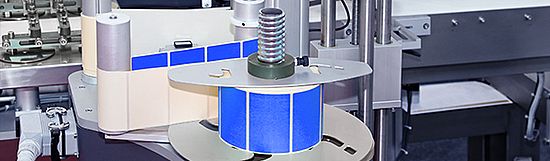
Direct drive frameless motors offer the ultimate in precision and torque density. But what if you could get these advantages in a motor that installs in minutes? Learn how we combined the performance of a frameless servo motor with the installation simplicity of a housed motor.
Simplify Your 3D CAD Design with these Downloadable Product Models

Simplify and accelerate your machine-design process. With Kollmorgen’s fully configurable 3D CAD models, you can search, configure and visualize more than 50,000 servo motor, drive and controller options, then download your selections for direct incorporation into your CAD design.
Enhancing Precision While Reducing Size, Weight and Cost
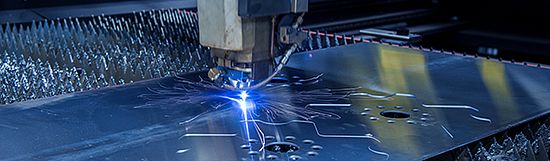
Learn how a manufacturer doubled the capacity of its precision laser-cutting machine without increasing the footprint — then expanded its market with a lower-cost version that still delivers excellent performance. What will your next machine be capable of?
July Training Events
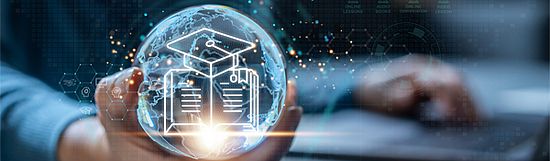
Register for the live session or to receive a link to the recording
Unlock the Secrets of Effortless Motion Control Programming
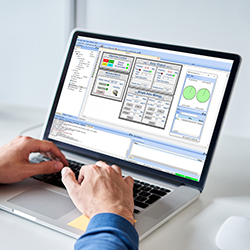
Thursday, July 11, 2024, 11:00 a.m. ET
Ever wish you could have one seamless tool for creating complex motion tasks — with integrated PLC programming languages, graphical definition of multi–axis relationships, simulated motion testing and more? Now you can. Take this tour to see how it all works.
Save My Seat
AKD BASIC Program Language Setup

Wednesday, July 17, 2024, 11:00 a.m. ET
Learn the easy way to set up and test motion programs on your AKD BASIC servo drive. Get a complete tour of our powerful Workbench software in this online training session.
Save My Seat
AKD BASIC Advanced Programming Loops
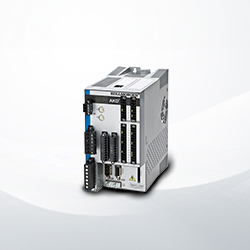
Thursday, July 18, 2024, 11:00 a.m. ET
Your AKD BASIC servo drive is capable of much more than basic motion tasks. Go online and learn how to create if…then…else and other conditional statements, create embedded loops, program interrupts and more using our powerful Workbench software.
Save My Seat
Resolving Servo Feedback Choices
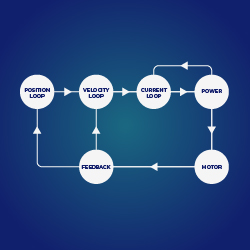
Thursday, July 25, 2024, 11:00 a.m. ET
A servo system can only be as precise as the feedback device. Making the wrong choice for your application can have devastating effects. Learn the operating principles and the pros and cons of each option, so you can achieve top performance with confidence.
Save My Seat
How to Ensure Motor Compliance in Exoskeleton Design
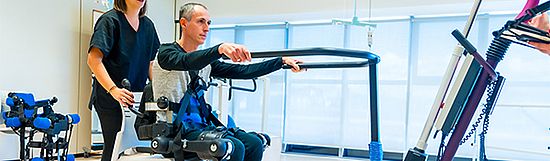
In the ever-changing field of robotics and wearable technology, exoskeletons hold growing promise in several applications — but bringing them to life can be challenging. That’s where optimized motor design comes in.
Tips for Selecting Stepper Motors and Drives

On Demand
You’ve determined that a stepper motor is the right technology for your application, but how do you choose the optimum motor and drive combination? With so many available options, this online session will explore the differentiating features and give you the selection tools and tips you need to make the right choice with confidence.
Enabling a New Standard of Performance for Stepper Motors
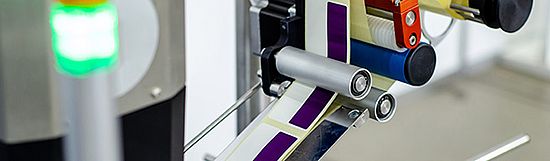
The P8000 series stepper drives deliver smooth, quiet motion across the full speed range — ideal for labelers, indexers, CNC machines, packaging machines, pumps and other applications requiring low-speed, point-to-point motion control for fixed loads.
PMX: The No-Compromise Stepper
When your design calls for high torque and perfect fit in a stepper motor, it calls for the PMX series. These motors offer great performance and quality in a wide range of standard frame sizes and standard options—all at a very affordable price point.
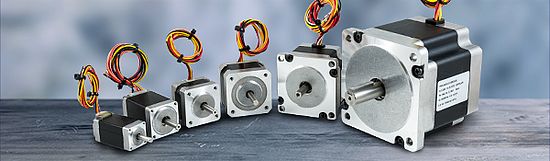
Optimize Your Stepper Now
Choose the right frame size, matched to your voltage, torque and speed requirements. It’s simple to get the application-specific performance you need with this online design tool. Try it.
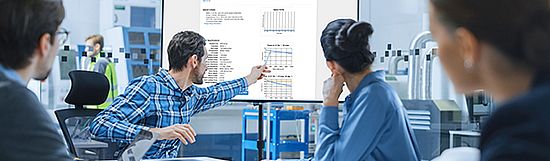
5 Critical Insights: Interpreting the Bode Plot
Bode plots reveal the unique frequency-response fingerprint of servo mechanisms. But how can you read the fingerprint and use it to fine-tune your system? Optimize machine motion by unlocking these five key Bode plot insights—complete with illustrated examples.
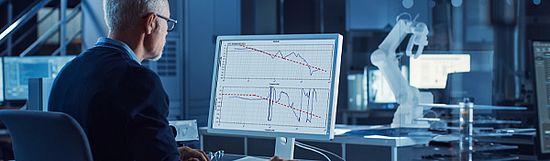
Motor Windings: Understand How They Work and Affect Performance
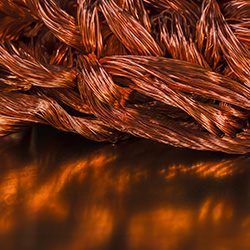
Friday, June 21, 2024, 11 a.m. ET
To maximize your application’s motion performance, specify the optimum servo motor. Stator windings play a major role in determining motor torque, velocity and horsepower. Join us online to enhance your engineering skills through an in-depth knowledge of motor windings.
Save My Seat
AKD2G Drive Quick Setup Guidance
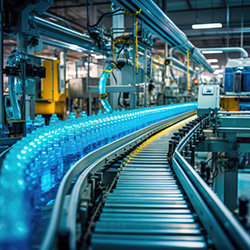
Wednesday, June 12, 2024, 11 a.m. ET
Join our online Mentor Session series to learn the quickest, most effective procedures for setting up and programming your AKD2G servo drive using our Workbench software. Accelerate your path to productivity.
Save My Seat
Advanced Configuration for AKD2G Dual–Axis Drives
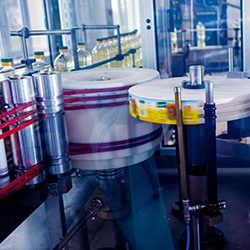
Thursday, June 13, 2024, 11 a.m. ET
Unlock the power of your dual-axis AKD2G drive, including triggering multiple motion commands with a single input, setting up functional safety features and much more. Join this informative online session, and master advanced dual-axis motion tasks.
Save My Seat
See Exactly How Your Motor Will Perform
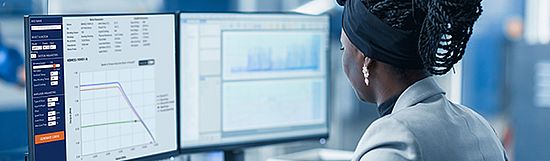
With just a few clicks, our Performance Curve Generator graphs the continuous torque, peak torque at different temperatures, and torque/speed characteristics of all our housed motors. There’s never been an easier way to evaluate the optimum motor for your application environment.
Building a Successful Surgical Robotics Company Through Customizable Cobot Design
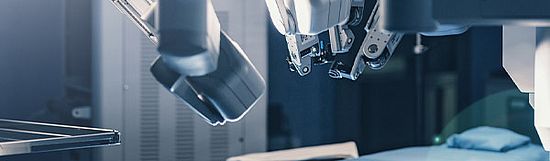
On Demand
Join Dr. Jindong Tan, the President and Founder Azure Medical Innovation, along with Gene Matthews, Kollmorgen Senior Product Manager as they discuss navigating through the unique challenges that are presented in the surgical collaborative robotics market. They will explore critical engineering considerations when specifying surgical application needs regarding collaborative features, AI integration in the surgical flow, and certification requirements.
AKM2G Servo Motors
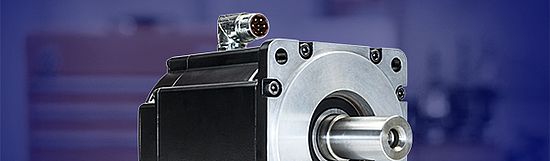
Get significantly more torque, increased feedback performance, reduced cabling and other next-generation capabilities—without changing your installation footprint. What will these motors do for your machine?
Tips for Scaling Exoskeleton Production
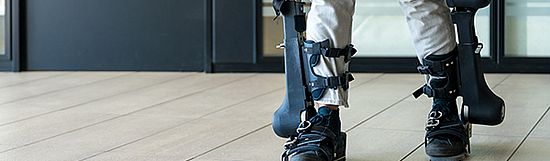
The exoskeleton market has been built on smaller volumes and custom production. But as the industry shifts — and exoskeletons become more common and viable for everything from medical rehabilitation and mobility to heavy load lifting — OEMs should be smart about the transition to efficient, high-volume production.
Motors Designed to Win the New Space Race
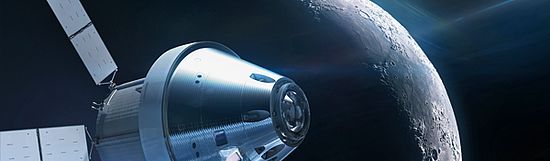
From powerful motors that move massive ground station antennas to radiation-hardened and outgassing-resistant motors for satellites and spacecraft, Kollmorgen supplies motors that deliver reliable motion in the most challenging space applications.
Automating Systems for Metal Forming
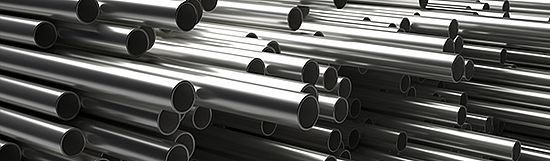
A builder of automated tube-cutting machines increased productivity by 20%, completely eliminated manual adjustments, and achieved unprecedented versatility to serve wide-ranging market needs. Learn how motion can transform your metal-forming machine.
Clean Mirrors for Clean Energy
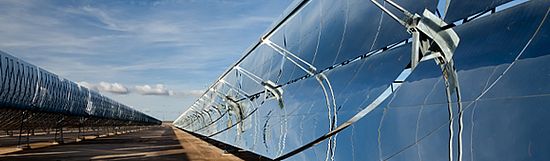
To keep energy flowing, heliostat solar plants need to keep thousands of massive mirrors clean. Learn how Kollmorgen motion helps increase maintenance efficiency by 500% and cleaning efficiency by 2,400% while operating in unpredictable terrain at temperatures often below –30ºC.
Tips for Selecting Stepper Motors and Drives
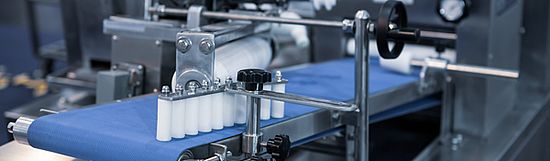
You’ve determined that a stepper motor is the right technology for your application, but how do you choose the optimum motor and drive combination? With so many available options, this online session will explore the differentiating features and give you the selection tools and tips you need to make the right choice with confidence.
The Difference Between Continuous Ratings and Holding Continuous Loads
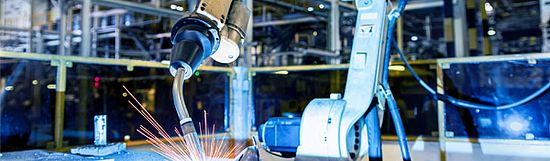
When a motion application requires holding a load in position for an extended time period, engineers encounter a lot of confusion around words like “stall” and a lot of uncertainty about proper servo motor sizing. Get clear answers and practical advice to ensure the success of your application.
ZF Servoplan - planetary gearbox
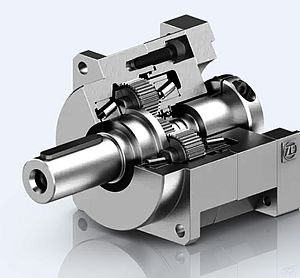
For a wide range of applications in engineering, ZF offers a complete range of planetary gearboxes for a wide range of applications and always perfectly adapted to the intended purpose.
What can Servoplan - planetary gearbox provide?
Servo-controlled transmissions can be used in several contexts. Single-speed and two-speed servo drives with ZF Servoplan gearboxes are used wherever highly dynamic and precise positioning is required. Target output torques of 25 - 3,000 Nm are possible with different model sizes. Planetary gear sets for servo motors are used in packaging technology, in forming technology, as well as in general for machinery and equipment.
Advantages:
- Special galvanic surface
- Permissible high acceleration torque
- Low gearbox temperatures and minimal power loss
- Without will
- Compact design
- Robust shaft seals ensure a permanent and secure seal
Motion for Missiles: From Speed of Innovation to Speed of Production
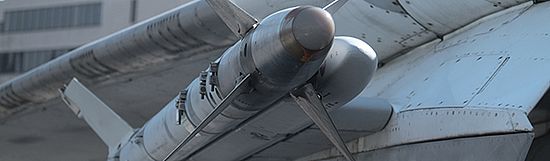
The worldwide demand for rockets and missiles is rapidly growing, and the most innovative designs will lead the market. How can you accelerate development of mission-critical guidance and control systems that depend on highly specialized motion systems? Kollmorgen has answers.
Improve Flexographic Printing Performance
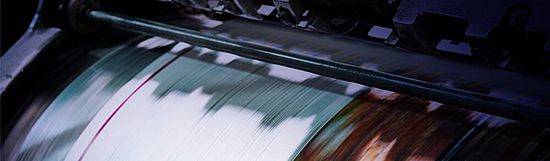
Flexographic printing has advanced significantly, but there remains untapped opportunity. Perfect motion synchronization can ensure consistent web tensioning, precise registration and steady repeat lengths. Learn how to apply direct drive technology to deliver higher-quality print jobs, faster.
The Key to Next-Generation Surgical Robots
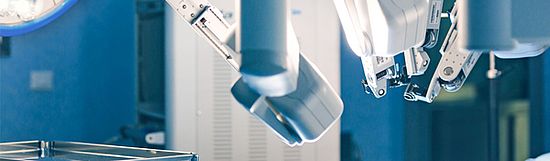
Surgeons want robotic cameras and instruments to operate as closely together as possible for an accurate field of view and minimal patient trauma. Learn how next-generation frameless motors are advancing the state of the art for high-performance, high-precision robots.
Unlocking Design Possibilities with Frameless Motors
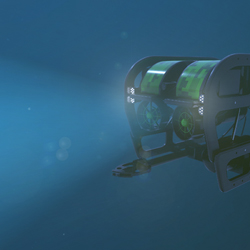
Friday, May 17, 2024, 11 a.m. ET
Frameless motors bring powerful and exciting new possibilities to a wide range of machine designs. Learn how to incorporate this transformational technology into systems that are lighter and more compact, more precise and reliable, and hardened against extreme washdown, underwater, radiation-exposed, high-vacuum and other challenging environments.
Save My Seat
Tips for Selecting Stepper Motors and Drives
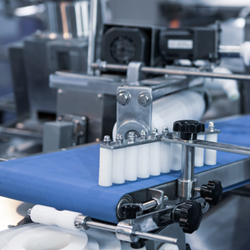
Thursday, May 9, 2024, 11 a.m. ET
Stepper systems offer performance and simplicity to suit a wide range of applications but selecting the optimum stepper motor/drive combination can be daunting. Join our online session to delve into the range of stepper technologies, their features and benefits, and the design tools available to help you make the right choice.
Save My Seat
Mastering Dynamic Motion: Revolutionizing Exoskeletons
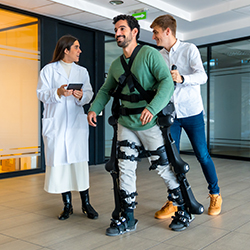
Wednesday, May 22, 2024, 11 a.m. ET
New innovations in exoskeleton design promise to bring transformative possibilities to military, logistics, healthcare and other applications. Learn how to navigate the unique mobility challenges involved, maximize motor efficiency, and ensure that your motion solution is highly manufacturable and scalable for marketplace success.
Save My Seat
MOOG miniature DC motors.
https://www.moog.com/products/motors-servomotors/brush-motors/cube-torque-brush-dc-motors.html
Our family of miniature permanent magnet cube brush DC motors includes motors available in 0.75 inch and 1 inch frame sizes. These motors are designed to suit a wide range of applications including direct drive servo systems, recorder drives, torque hold and high torque, low speed control systems. It is a motor with fast response at all operating speeds due to its high torque-to-inertia ratio and low self-inductance. Torque increases directly with input current for linearity. As a direct servo drive, it offers high resolution. Its cubic shape allows weight and space savings and easy assembly.
Cube motors are often used in applications where high torque is required but available space is limited. Cube motors are easier to mount than cylinder motors in many applications and are easier to lock into the housing.
Moog offers a choice of Alnico or Samarium Cobalt magnet materials to meet most requirements. These rare earth magnets produce higher magnetic energy per unit volume than most commercially available permanent magnets. Alnico magnets provide increased temperature stability, while Samarium Cobalt magnets offer high energy with good, stable performance.
We are equipped for hundreds of designs with different windings, terminations and other options including gears, brakes, resolvers, encoders and potentiometers. Most of the designs can be easily adapted to different requirements. We can also provide customized engineering services
Integrated brushless DC motor MAC320-P for OEM machines from JVL
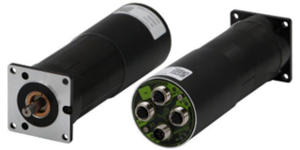
https://www.jvl.dk/1328/mac320
320 W MAC motor® - Double the power but SAME size - with a new generation absolute multi-turn encoder, based on
Wiegand principle (harvest) where no battery is needed!
JVL has developed a new addition to our Mini-MAC series. Servo motor MAC320 - 320 W.
We have developed our most powerful integrated motor in the NEMA23 size.
The target application is high-performance positioning in a small all-in-one package.
Key features
- Twice the power - but SAME size as the MAC141 (134W)
- Very high torque to volume ratio
- Special DC brushless motor for OEM applications
- 3 times the maximum torque (1 kW)
- Recommended supply voltage 48 VDC from PSU or battery
- An absolute multi-turn encoder option. No battery or equipment required
- Use standard JVL expansion modules for Ethernet, CAN bus and PLC applications
- Option for STO connector
- The ø8 mm shaft can handle higher torque and power
- Position accuracy ±0.065°. With multipole encoder ±0.037°
- Absolute encoder singleturn 13bit. Absolute 19 bit
What is new?
Absolute multi-turn encoder based on collection technology without battery or device
High performance Ethernet similar to larger MAC engines
New MOSFET technology for higher efficiency and cooler motor
Encoder resolution 8192 CPR (higher resolutions planned)
Options: STO and/or brake connector
More advanced FOC filter for lower noise and better engine performance
The high performance is due to the high magnetic forces, which on the one hand create a high torque of the shaft, but the trade-off is a high torque of the gears.
It is therefore not possible to achieve the same level of speed accuracy compared to other MAC engines. This is usually of no consequence for positioning applications.
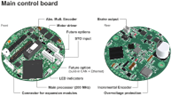
Design a More Capable UAV
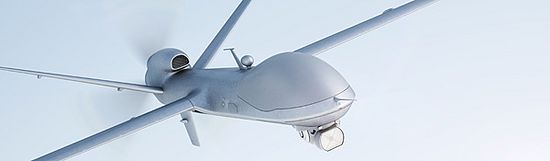
From precise actuation of flight-control surfaces to positioning of visualization systems, payloads and more, the optimum unmanned aerial vehicle design incorporates motors that operate at peak efficiency while minimizing size and weight. Learn how to specify the ideal, flight-worthy motor for each UAV application.
Deliver High Performance in a Compact Form withTBM2G Frameless Motors
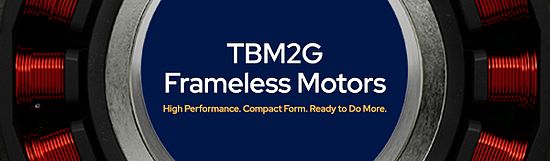
With significantly higher torque density in a more compact axial design, next-generation TBM2G frameless motors are ready to perform, ready to fit your design, and ready to scale. Learn how you can engineer a more capable machine, without compromise.
Monitoring and Controlling Brakes Through On-Drive Functional Safety Technology
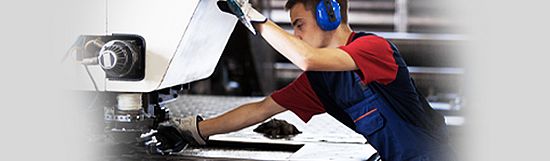
Without proper brake monitoring and testing, vertical loads can be hazardous. However, ISO 13849-1 does not allow brake testing functions to be embedded into standard machine controls. Learn the simple way to comply while achieving the safety level you need.
Discover the Power of Kollmorgen Automation Suite™
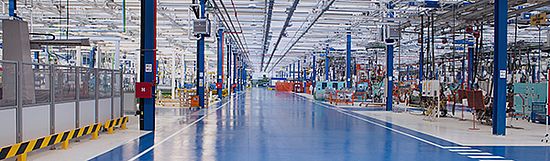
With controllers, drives, motors, communications and programming tools designed to work together, you can engineer more capable automation solutions. We put all the pieces together in one suite designed to make development of exceptional machines faster and easier.
High Performance Machine Control Made Easy with Kollmorgen Automation Suite
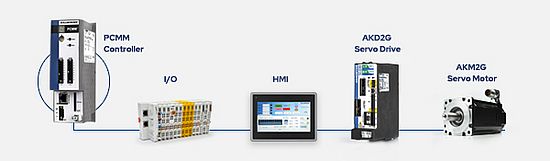
On Demand
Learn how the complete automation solution, Kollmorgen Automation Suite, can help you bring truly differentiated machines to market faster. Join our KAS training session online and simplify your development of high-performance machine control.
Online, Interactive Product Selectors
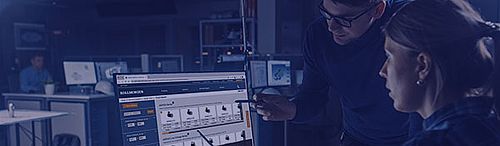
From torque, speed and power to form factor, controls and accessories—the perfect fit is key to your application’s success. Use our selection tools to choose motion products with confidence. Our instructional video shows you how simple it can be.
Electric Actuation Is Replacing Hydraulics. Are You Ready to Make the Move?
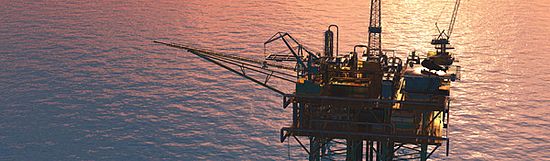
For hundreds of years, hydraulic actuation systems have been making noise, wasting energy, leaking and requiring constant maintenance — all to achieve imprecise motion over a limited range. For most of that time, they have been the only real choice for powerful actuation. But now there’s a better way. Learn the advantages of electric actuation and how to make the transition.
Easy-to-Clean, Durable Motion Systems for Food Processing and Packaging
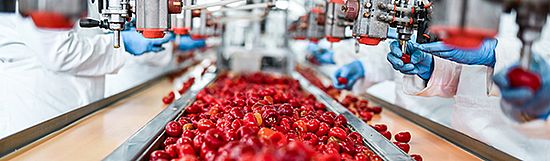
The need to safeguard the food supply against disease-causing pathogens is absolute. But food processors and packagers struggle to keep machines sanitary while also maximizing productivity. Learn how smart component choices can enable direct washdown without damaging motors or other equipment, while leaving pathogens no place to hide.
Accelerate Humanoid Robot Development
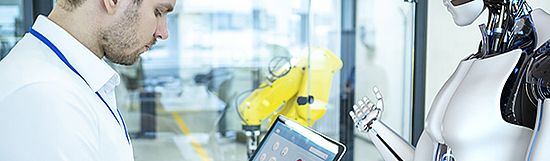
Designing and building a humanoid robot is challenging enough. But ensuring that it is manufacturable and marketable requires a new approach to creating multi-axis motion. Get your design right from the start with these three best practices.
Adjusting Standard Motion Profiles to Optimize Operating Speed and Time
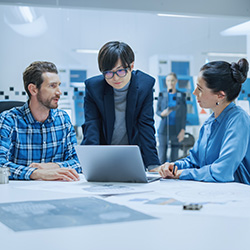
Thursday, April 18, 2024, 11 a.m. ET
The simplest and most commonly used motion profiles don’t always provide optimum results. Learn simple adjustments you can make to achieve the ideal speed and move time for your application — without the need for guesswork or extensive trial and error.
Save My Seat
Expand Machine Capability with Programmable Steppers Drives
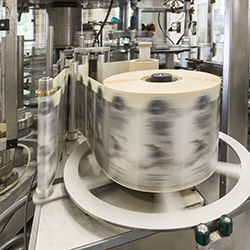
Thursday, April 25, 2024, 11 a.m. ET
Discover the future of stepper drive setup and operation. Kollmorgen Space software simplifies programming, lowers total cost and enables new closed-loop monitoring and control capabilities. Learn how it works in this online guided tour.
AKD2G Servo Drive Update Offers More Flexibility and Protocol Focus Than Ever
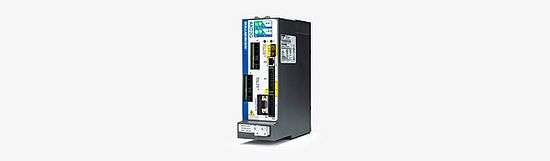
Our updated AKD2G servo drive — part of our 2G Motion System — features enhancements to our existing communication protocols, adding CIP Sync functionality for Ethernet/IP and PROFINET IRT for PROFINET. The expanded offering delivers easier integration with third-party controllers, easier setup and functional safety options.
Intentional design. Streamlined setup. Ultimate performance.
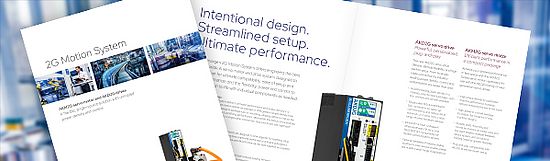
The Kollmorgen 2G Motion System offers engineers the best of both worlds: A servo motor and drive system designed to work together for ultimate compatibility, ease of setup and higher performance; and the flexibility, power and control to bring any design to life—with individual components as needed.
Kollmorgen and Stereotaxis Advance the Precision and Safety of Surgical Robots
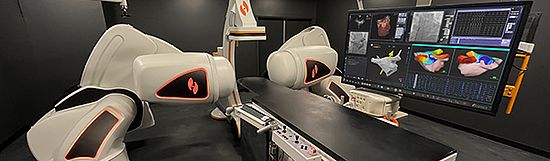
The new Genesis surgical robot is revolutionizing cardiac ablation procedures, giving patients the promise of longer, healthier lives. Learn how Kollmorgen technology and expertise made the difference for a visionary surgical robotics company.
TBM Frameless Servo Motors
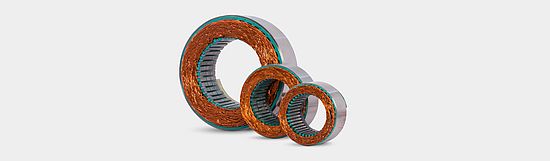
TBM Series servo motors offer a direct drive, frameless design embedded directly into your machine, delivering exceptional torque and precision while eliminating backlash and maintenance issues. Find the features and options that best fit your application.
Helping You Make Extraordinary Design Possible
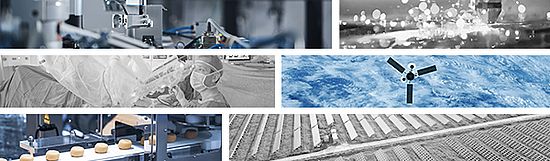
From factories and warehouses, to operating rooms and imaging centers, to energy production and space exploration, our motion technology and expertise enables our partners to solve the world’s toughest motion and automation challenges. Discover what we can do for your next project.
Motion for Missiles: Optimizing Performance
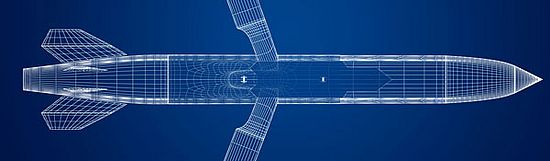
The electric motors that control missile fin actuators, seeker head gimbals and other mechanical systems must perform with absolute reliability. With a rapidly growing need for advanced weapon systems, learn how to specify motors that can perform reliably even in the most extreme conditions.
Frameless Performance, Made Easy
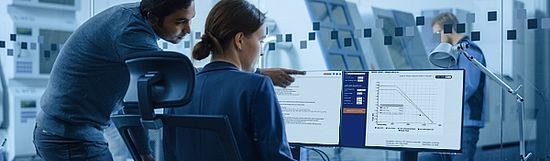
Optimize your frameless motor by simply entering your application requirements. This Interactive Performance Curve Generator does the rest, automatically.
Frameless Motors to Fit Any Application
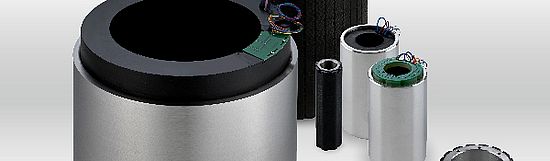
Embedded into your machine and driving the load directly, KBM frameless servo motors deliver optimum torque density and precision in the most compact package. Browse motors that deliver continuous power up to 20.1 kW and peak torque up to 12,812 Nm in frame sizes ranging from 60 mm to 850 mm OD. Find the ideal fit for your application.
From the Factory to the Farm: Washdown Servo Motor Technology
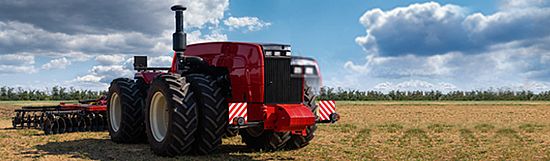
A new era of agricultural innovation is at hand. The same high-performance, washdown-capable motors used in food, beverage and pharmaceutical production promise to transform the productivity and profitability of farming automation. Learn why.
Sizing & Selecting Servos: Understanding the Need for a System Solution
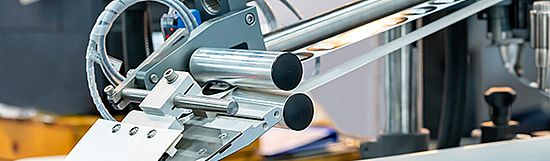
There are many parameters and variables to consider when sizing and selecting servo system components for an application. To simplify the process and maximize success, learn how to incorporate mechanical load, motion profile, ambient environment, cabling and other considerations into a system-wide approach.
Smart Technologies for Food Packaging Performance
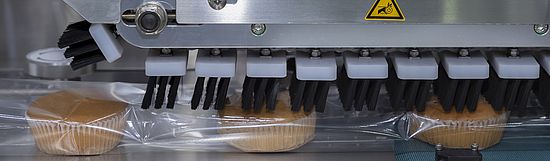
Today’s food packagers are looking for machines that are more compact and automated, driving greater throughput and accuracy. However, it can be challenging to achieve these goals using individual components that were designed with little regard for integration. Learn a smarter approach — building machines with much of the integration built in at the component level.
Maximize Missile Performance with Advanced Frameless Motors
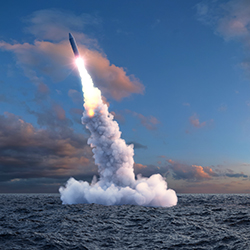
Tuesday, March 26, 2024, 11 a.m. ET
Missile manufacturers are under pressure to design and produce ever more sophisticated systems in greater quantities. Learn how to optimize missile guidance and control systems with a solid understanding of the frameless motor design principles that make a difference for actuator size, weight, performance and reliability. Join this informative online training.
Save My Seat
The Foundations of Electric Motion: Motion 101 Online
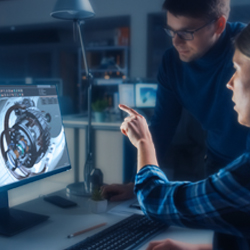
Wednesday, March 20, 2024, 11:00 a.m. ET
Learn the details of different motor types, open vs. closed loop control systems, and how to configure the optimum motion system for each machine axis.
Save My Seat
The Foundations of Motor Performance: Motion 101 Online
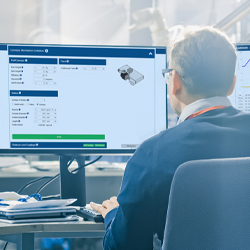
Thursday, March 21, 2024, 11:00 a.m. ET
Understand the role of feedback type and resolution as well as the influence of inertia, so you can meet your motion performance goals with confidence.
Keep Your Field Robot on the Job Longer, Working Stronger
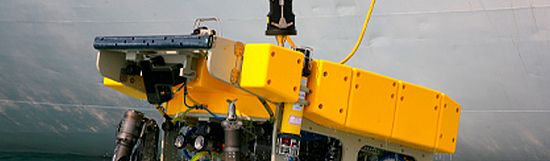
Robot-ready motors designed for optimum size, weight and efficiency in specialized applications can extend your field robot’s operating time, range and reliability. Learn how to engineer greater success for the robots that perform difficult jobs while keeping humans safe.
Improving Food Safety and Packaging Machine Reliability
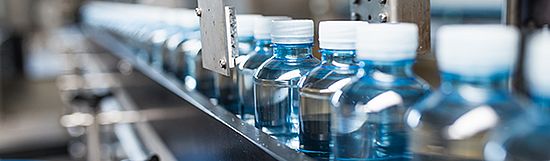
Food safety regulations are stricter. Consumers are more demanding. Competition is tighter than ever. How can you keep your food processing and packaging machines clean while minimizing washdown-related downtime and equipment failures? Learn proven methods for ensuring a safe food supply while maximizing the yield of your production line.
The Right Motor for Tough Conditions
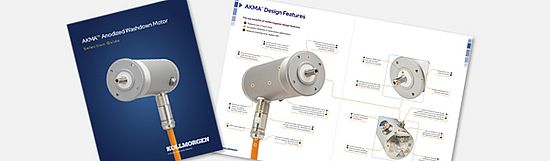
Whether you’re designing for tough, medium or heavy washdown applications or all-weather conditions, AKMA motors offer the ideal feature set. See which AKMA motor meets your unique specifications with our streamlined selection guide.
Calculating the Total Value of Hygienic Machine Design
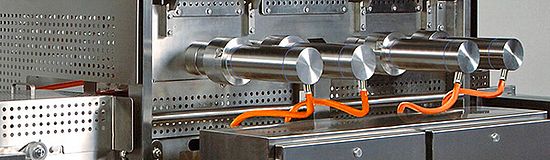
How do you know when designing with a high-performance servo motor that provides superior hygiene and reliable operation in demanding washdown environments is worth the investment? Learn how the patented design of our stainless steel AKMH hygienic servo motors helps improve your overall equipment effectiveness (OEE).
Powering a Submersible Robot for In-Service Inspection of Fuel Storage Tanks
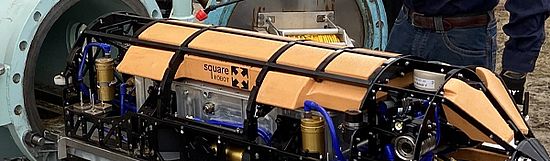
Why drain a massive fuel tank so that humans can enter and inspect it, when an innovative submersible robot can do it more efficiently, more cost effectively, while keeping people and the environment safe? Learn how Square Robot used highly modified frameless motors from Kollmorgen to help make this extraordinary new technology possible.
Motion for Medical Imaging: Proven Processes, Reliable Delivery
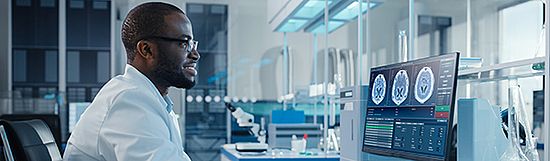
Medical imaging systems require precise, powerful, perfectly controlled motion. Learn the proven, structured development process that can help ensure success — in the procedure room and the marketplace. Count on collaborative expertise, superior performance, dependable supply and global support.
See the Latest Addition to the P8000 Lineup
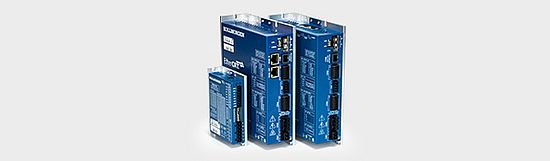
Expanding on the successful P8000 stepper drive family, the new P80360-ECE features an EtherCAT communication interface that supports cyclic synchronous position (CSP), cyclic synchronous velocity (CSV), profile position, profile velocity and various homing modes. Users can integrate the P80360 stepper drive into existing EtherCAT ecosystems — enabling real-time control for increased throughput and machine capability.
Put Your UAV on the Trajectory of Success
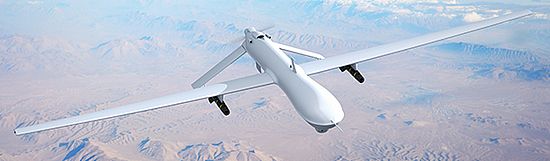
When the mission matters, your UAV must be designed and built to go the distance. Learn how motion solutions designed specifically for flight can minimize size and weight while maximizing torque and efficiency. Fly longer and farther with Kollmorgen.
Servo or Stepper Motor: Which Should It Be?
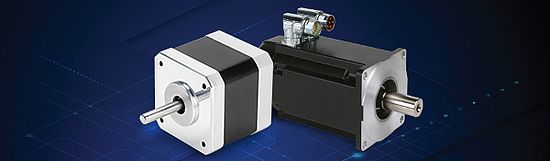
Servo and stepper motors are both great technologies for moving and positioning loads. But they operate in different ways, and it’s important to make the right choice for your application. Learn how these motors work, the value of each, and how to select the technology that will help your machine achieve its full potential.
We’ll Help You Design and Deliver a Better Machine
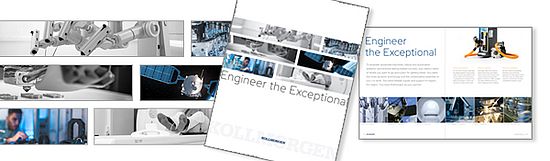
To win the future, machines, robots and automation systems need to achieve higher levels of precision and performance. Kollmorgen’s dynamic motion products, collaborative engineering expertise, and global delivery and support can help move your business to the front of the pack. Learn how we do it.
For 2024, Autorotor has improved some new accessories for rotary tables and indexing rotary tables
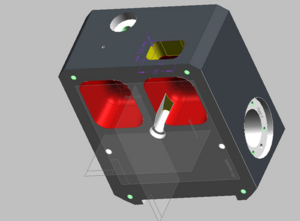
For turntables:
- special central hole for routing cables or pipes.
- central support, where it is possible to fix the turntable or other parts of the machine
For indexing circular tables:
- a central support, where it is possible to fix the rotating plate or other parts of the machine
- supports for the unit
Accelerating the Development of Prostheses and Exoskeletons
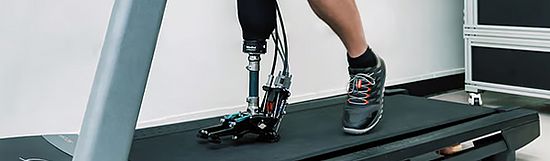
An innovative test-bed platform developed by Humotech delivers the torque, speed and responsiveness needed to evaluate and refine wearable designs in actual human use, accelerating the prototyping process and helping improve results. Learn how.
From the Factory to the Farm: Washdown Servo Motor Technology
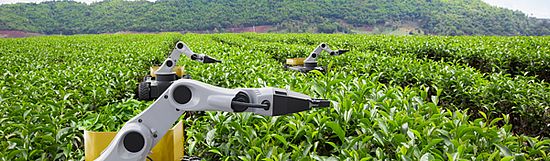
High-performance motors that withstand direct washdown can dramatically increase equipment reliability and productivity. Learn the advantages that agricultural automation is borrowing from today’s factory floor.
Interactive Product Selector Tool
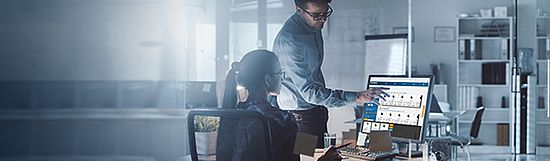
There’s no need to search through websites or catalogs looking for a perfect fit. Our online Product Selector tool does the research for you. Simply enter the torque, speed, power, size, and other requirements and be guided to motors, drives and cables that best suit your application.
February Training Events
Register for the live session or to receive a link to the recording
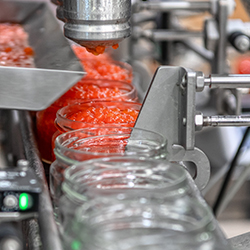
Ask The Experts Webinar: Motion Control for Food Packaging
Ask The Experts Webinar:
Motion Control for Food Packaging
Thursday, February 8, 2024, 11 a.m. ET
The need for frequent, high-pressure washdowns can reduce productivity and damage equipment. How can you clean motors directly — without the need for shields or bags, and without the risk of harmful water ingress? Get answers to your specific questions for achieving reliable motion control in hygienic food packaging environments.
Save My Seat
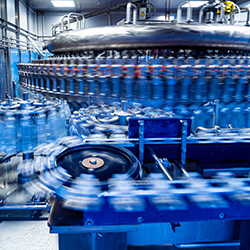
Simplify Regen Resistor Selection for Motion Systems
Thursday, February 22, 2024, at 11:00 a.m. ET
A regeneration resistor captures the excess electrical energy that is generated during motor deceleration. Dissipating this excess energy can prevent potential damage to your motion system. Join this online session and learn how to optimize your regen resistor for greater system reliability.
Save My Seat
Motion Innovation for Energy-Efficient Metal Forming

Learn how Kollmorgen’s newly patented technology and expertise helped the world’s #1 manufacturer of sheet-metal bending machines, Salvagnini, improve energy efficiency, performance and usability in harmony with the company’s core values.
Motion Control Fundamentals for Humanoids & Exoskeletons
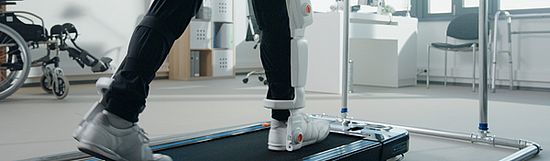
Humanoid robots and exoskeletons are bringing new possibilities to healthcare, manufacturing, construction and service industries. Learn how to improve upon human capabilities with precise, powerful, efficient motion — and how to maximize commercial success.
Make Any Medical Imaging System Better
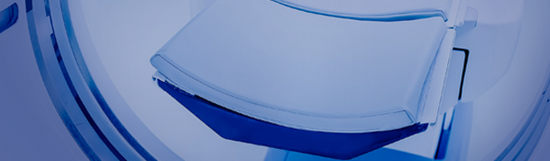
CT, MRI, hybrid, digital mammography and nuclear medical imaging. Fixed systems, mobile X-ray and ambulatory medical imaging centers. They all depend on the right motion for the right modality. Learn how to get it right.
TBM2G Motors for Simply Better Design
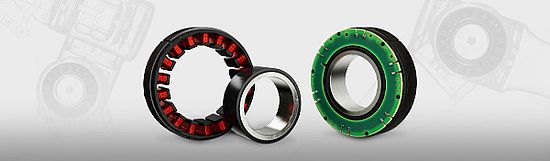
Design and build a more compact, efficient, higher-performing robot. TBM2G frameless servo motors are specially created to meet the unique requirements of cobot, surgical and humanoid robot joints, providing a custom-like fit while ensuring manufacturability with long-term availability and support.
Frameless Motor Performance Curve Generator
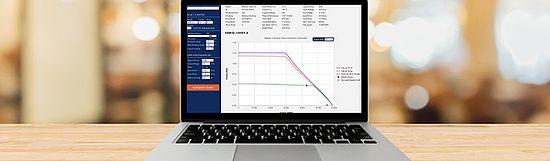
Map speed-torque curves based on variables including current, voltage, ambient temperature and winding factors. It’s easy to specify the optimum frameless motor for your application using the online Performance Curve Generator.
On-Demand Webinar: Optimizing Form Factor With the D2L Rule
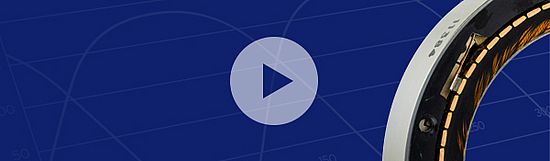
The length and diameter of your motor have dramatic effects on stabilized platform performance. Learn how to apply this rule to size the most compact motor.
We’ll Help You Design and Deliver a Better Machine
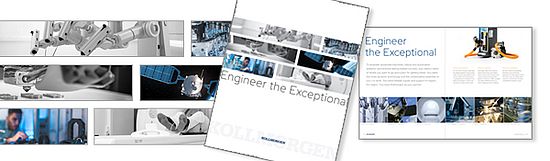
To win the future, machines, robots and automation systems need to achieve higher levels of precision and performance. Kollmorgen’s dynamic motion products, collaborative engineering expertise, and global delivery and support can help move your business to the front of the pack. Learn how we do it.
Humanoid Robots: From Design to Delivery
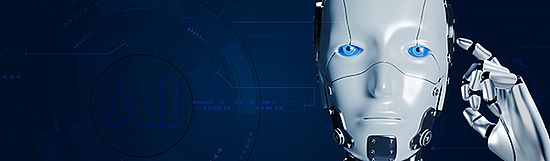
In any engineering project, time and budget constraints at the prototype stage can lead to excess costs and delays when scaling up to full production. Learn how to design for both performance and manufacturability, beginning with the prototyping stage, to accelerate your time to market and maximize your prospects of success.
The Difference Between Continuous Ratings and Holding Continuous Loads
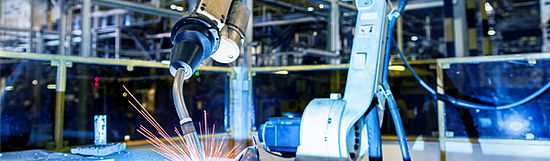
When a motion application requires holding a load in position for an extended time period, engineers encounter a lot of confusion around words like “stall” and a lot of uncertainty about proper servo motor sizing. Get clear answers and practical advice to ensure the success of your application.
Preventing Electromagnetic Interference in Servo Cables
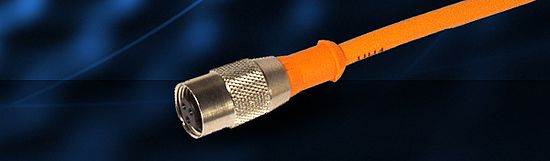
Available On-Demand
Power cables can cause electromagnetic interference that corrupts the position and velocity signals carried by nearby feedback cables. Learn how to tame EMI and ensure predictable servo motion.
Efficient and Effective Risk Management for Vertical Axes
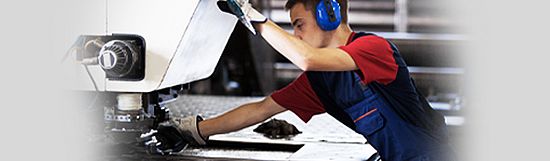
With new safety standards that require periodic brake testing and prohibit embedding of test functions within standard controls, what’s the best way to keep operators safe, maximize productivity, and simplify machine design? Learn the advantages of on-drive safety functions.
AKM2G Servo Motors
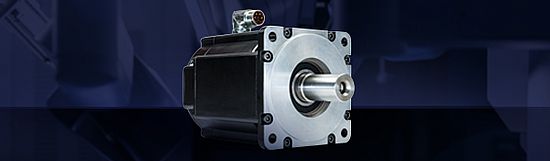
Get significantly more torque, increased feedback performance, reduced cabling and other next-generation capabilities—without changing your installation footprint. What will these motors do for your machine?
Size Your Motor and Drive in Minutes
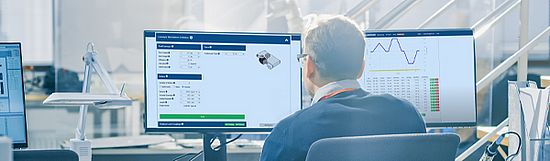
Keep it simple. If you know your application requirements, the Motioneering tool will guide you to the motor and drive pairings that best fit your needs.
Improving the Precision and Productivity of Lithium-Ion Battery Coaters
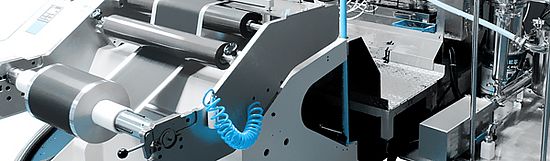
Through the rapid growth of electric vehicles and other battery-powered products, lithium-ion batteries are changing the world. Battery manufacturers are under intense pressure to increase quality and yield. Learn how a battery pole-coating machine achieves micron-scale accuracy and 33% higher throughput.
Compact Joint Design for the Next Generation of Surgical Robots
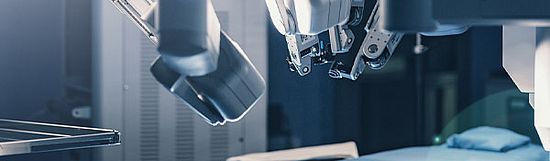
In robot-assisted procedures, surgeons value the ability to place multiple instruments in a nearly parallel orientation. Learn how to design compact robotic arm joints that give surgeons the dexterity they need and help improve patient outcomes.
5 Easy Steps to Better EO/IR Motion
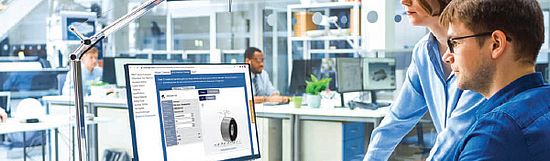
A successful EO/IR program depends on efficient prototyping, cost-effective production and reliable supply. Don't let customization problems derail your project. We'll show you how to get exactly what you need in a standard or easily modified motor.
Your Agricultural Robot Can Be More Productive
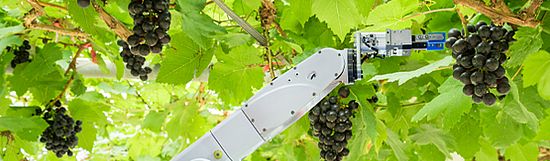
New agricultural robots can perform almost any task human hands can do — but much faster, working night and day without rest. Learn the motion technologies and choices that can help your robot reach its full potential for productivity and profitability.
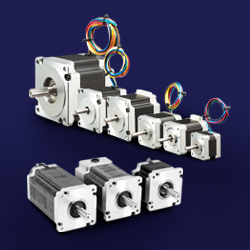
Tips for Selecting a Stepper Motor On Demand
With the wide range of stepper motor options, how do you select the right motor for your application? In this session, Kollmorgen experts cover the key differentiators in stepper motor technology and help you choose the best options for your application.
Watch Now
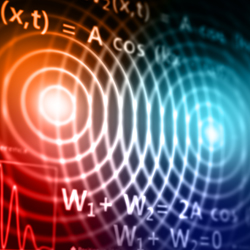
How to use grounding, shielding, and Bonding to Reduce
Electromagnetic Interference (EMI)
On request
Mitigation of electromagnetic interference is essential to maintain accurate movement without surprises. Find out why shielded cables are important, how to ground cables properly, and how to verify that your grounding is working properly.
Watch now
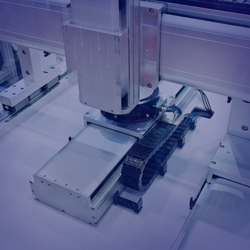
Motion control sizing and programming tips for gantry applications
On request
Because you need to synchronize movement across multiple axes, designing and implementing a portal application can be particularly challenging. Learn special considerations, product sizing methods, and motion programming techniques that guarantee success.
Watch now
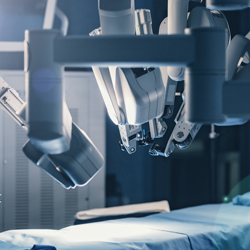
Like a customizable Cobot design It can help you build success Society of Surgical Robotics
On request
Join Dr. Jindong Tan, President and Founder of Azure Medical Innovation, along with Gene Matthews, Senior Product Manager, Kollmorgen, as they discuss navigating the unique challenges presented in the surgical collaborative robotics market. They will explore critical technical aspects in specifying the needs of surgical applications regarding collaboration features, integration of AI into the surgical flow, and certification requirements.
Watch now
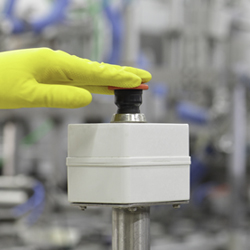
Differentiating braking techniques for your servo system
On request
Correct braking by servomotor is essential for the safety of employees while maintaining production requirements. But how do you choose which braking technique is right for your application? This session explores applications for safe, dynamic and safe dynamic braking.
Watch now
Discover Compact Motors with Big Performance
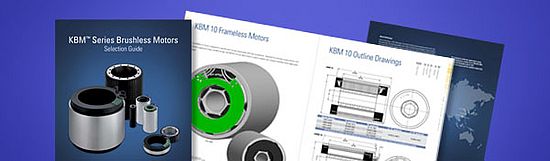
Frameless motors allow you to design a lighter, more compact machine with the precision of direct drive. Directly embedded in your machine’s own housing, they’re ideal for reliable performance in the most rigorous environments. Explore the possibilities.
Implementing and Installing Frameless Motors
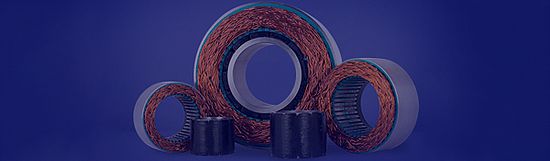
With frameless motors integrated directly into the mechanical structure, your machine can be more compact, efficient and dynamic. In this on-demand webinar, Kollmorgen specialist Tom S. Wood shows you how to solve the most common design challenges.
Frameless Performance, Made Easy
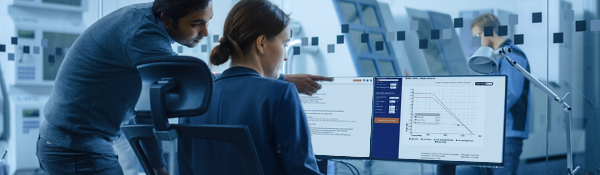
Optimize your frameless motor by simply entering your application requirements. This Interactive Performance Curve Generator does the rest, automatically.
Kollmorgen and Stereotaxis Advance the Precision and Safety of Surgical Robots
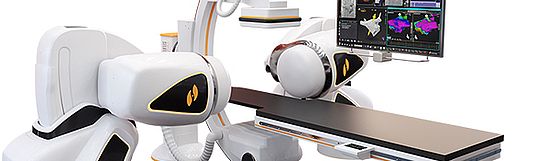
A pioneer in surgical robotics envisioned a new paradigm for performing more precise and effective cardiac ablations, but success would require advanced motion capabilities and collaborative engineering expertise. Learn how Kollmorgen helped bring the Genesis surgical robot to life.
It’s Time to Consider the AKM Servo Motor
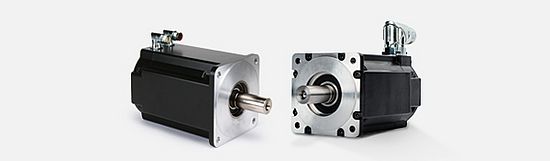
The AKM series of servo motors has always been a top performing motor for our customers. Now with improved lead times as short as 2 weeks on some motors, it’s time to give us a call to see if we can help with your machine design too.
Stop, Hold and Go Safely: Motion Tuning for Vertical Loads
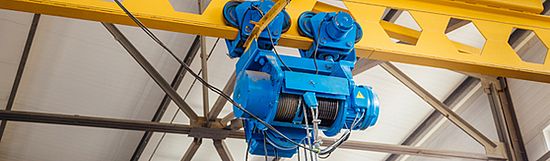
Gravity never compromises. When vertical load safety matters, neither should you. Learn how to tune your vertical axis right the first time and ensure reliable operation every time with this helpful guide covering braking physics, safe brake control, safe brake testing and more.
Stop Dynamic Loads with Confidence
Learn how the AKD2G servo drive Safe Dynamic Brake Calculator can help you properly size your system without the need to repeatedly buy and test components. Speed development time and save money while ensuring accurate, timely braking.
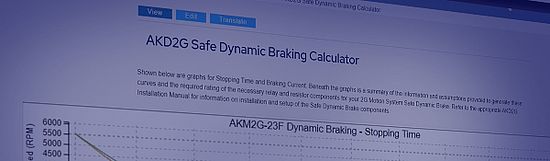
Efficient and Effective Risk Management for Vertical Axes
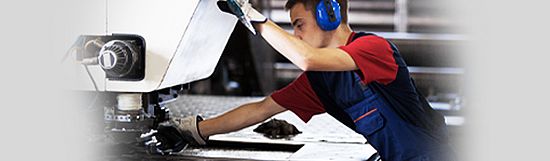
With new safety standards that require periodic brake testing and prohibit embedding of test functions within standard controls, what’s the best way to keep operators safe, maximize productivity, and simplify machine design? Learn the advantages of on-drive safety functions.
Machine Safety: The New Era of Protection and Productivity
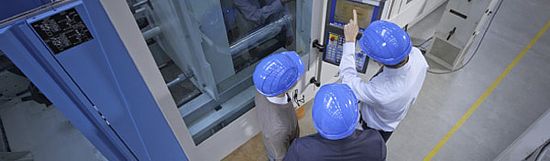
Learn the evolution of machine safety—from cages and disrupted production to light curtains and continuous production. Now you can eliminate shutdowns without putting operators at risk.
The best integrated motors in the world
World's most compact integrated 4.5 kW
servo motor - 13.5 kW peak
Controller, PLC, encoder, power supply, industrial Ethernet and built-in switch integrated in one unit
SPS - Smart Production Solutions | Hall 4 Booth 301 | Nuremberg, 14.-16. November 2023
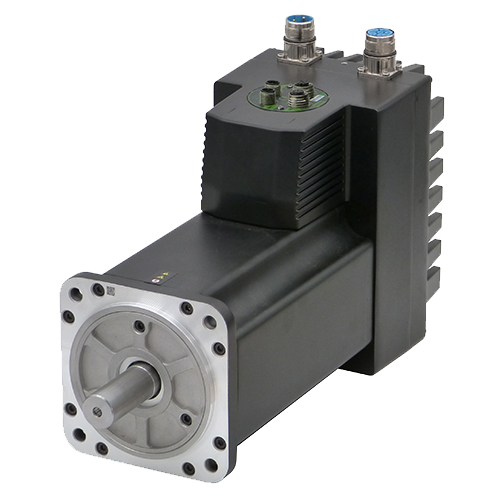

Contact JVL for a free e-ticket
Get your free ticket now, simply by contacting JVL. We will then send you a ticket code.
It is a great opportunity to meet JVL and discuss your application and requirements.
Book a meeting with JVL
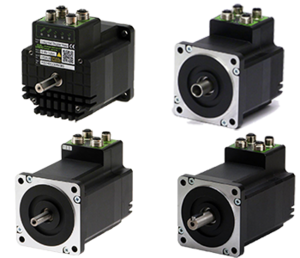
ServoStepTM in size NEMA34 keeps expanding
Large variety of shaft versions: Ø9.53 mm, Ø14.0 mm, double shaft, hollow shaft and now also Ø12.7 mm.
Market leading resolution of 409600 counts/rev
Optional Ethernet protocols and possibility to daisy-chain Ethernet cables from motor to motor.
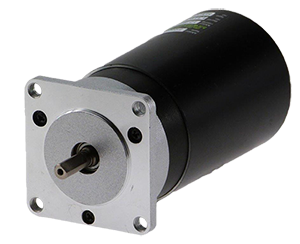
High power positioning in a small all-in-one package
The new integrated servo motor MAC083 offers 83 W / 4000RPM at 24VDC and 250W peak.
This makes it the most powerful integrated motor in the NEMA23, length 110 mm.
Optional with absolute multiturn encoder based on the Wiegand principle where no battery is needed.
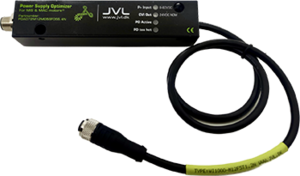
Power Supply Optimizer
New combined power dump and 24VDC control power supply.
Has your power supply shut down during braking?
Braking produces problematic return energy.
The new power supply optimizer is designed to address this problem, by adding a built-in power dump circuit to the power cable.
It greatly improves protection of both the motor and the power supply.
- Built-in 24 VDC control power supply for CVI when using 48-72 VDC.
- Adapts automatically to the voltage level.
- Easy plug-n-play, no settings needed

320 W Stainless Steel Servo IP69K
MAC231 - All-in-one Integrated servo motor in stainless steel and IP69K. Ideal for harsh environments.
Protected against both high pressure and high temperature washdowns.
320 W RMS power S3 with 25% duty cycle and 750 W peak. 50 Nm with optional built-in gearbox.
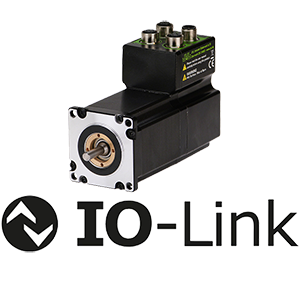
IO-Link
JVL can now also connect to IO-Link via our new IO-Link Gateway which can be used on both our MAC motor® integrated servo motors and ServoStepTMintegrated stepper motors.
IO-Link is a cost effective alternative to industrial Ethernet.
For ServoStepTM you can additionally run 2-5 motors on 1 pcs IO-Link Gateway using multidrop, reducing cost even more.
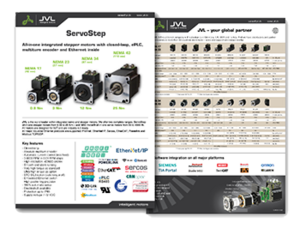
ServoStepTM range
JVL supplies integrated stepper motors with closed-loop, ePLCTM, multiturn encoder and Ethernet inside.
NEMA17-43 (0.18-25Nm)
Read more about all the options in the flyer
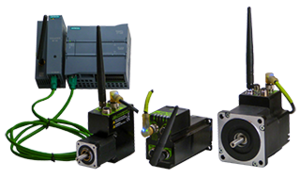
Industrial Wireless Ethernet
Supporting both EtherNet/IP, Profinet and ModbusTCP/UDP, JVL can now deliver wireless Ethernet for the whole range of ServoStep motors, NEMA17-43.
Set up your motors as Client or Access Point, using 2.4 GHz or 5 GHz.
To avoid cabling, use a battery for motor power. Combined with the closed-loop feature an energy saving of 93% can be reached.
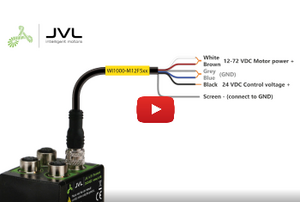
Quick power connection guide for MIS17-43
In just 3 minutes you get all the important information about how to connect JVL's ServoStepTM motors NEMA17-43.
You learn the basic specifications, color coding and about pitfalls to avoid.
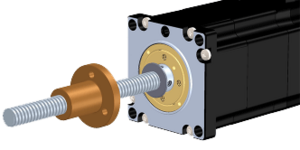
New shafts for direct mount
NEMA23 motors are now available with hollow shaft or oversized shaft. Both motor types have large double row ball bearings so you can directly mount a spindle or timing belt wheel. No coupling needed.
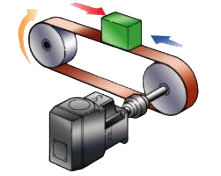
MotorSizer 4.0 sizing tool
With the free JVL software MotorSizer you can calculate and show the combinations of motors and gears that can run the application according to your specifications.
Possible types of drive set-ups include:
- A belt driven application
- A ball screw application
- A rotary disc application
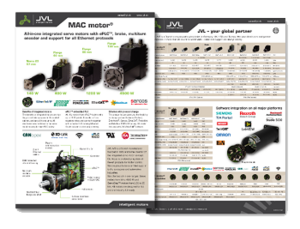
MAC motor® range
JVL supplies integrated servo motors with ePLCTM, brake, multiturn encoder and support for all Ethernet protocols.
50-4500 Watt.
Read more about all the options in the flyer.
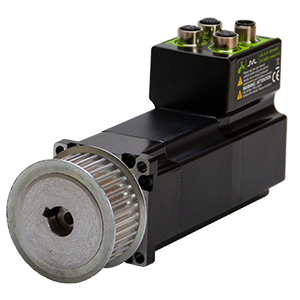
Motor for direct mount of a timing-belt wheel
The new MIS23xx49 ServoStepTM motor features a large Ø14 shaft and double row ball bearing.
The oversized bearing allows high radial forces directly on the motor shaft - up to 5100 N.
This combination can shorten your overall design length and save you the cost of an additional bearing housing.
The ServoStepTM motor is an all-in-one unit with embedded ePLCTM and 2 port Ethernet switch.
eVTOL Motion, From Design to Delivery
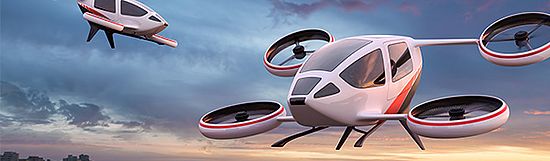
Did you ever imagine you could take an air taxi from the airport to a downtown location? Or see road congestion give way to direct, point-to-point delivery of goods overhead? With innovative eVTOL technology, all this and more could come true sooner than you thought. Learn how Kollmorgen is helping.
The Right Motor For Tough Conditions
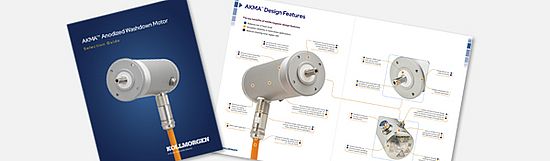
From its anodized aluminum coating to a vented design ideal for medium and heavy washdown applications, lightweight AKMA motors offer reliable performance when directly exposed to harsh environments. Use this guide to ensure the optimum AKMA fit and performance for your application.
Increasing Trajectory Welding Speed in Lithium-Ion Battery Production
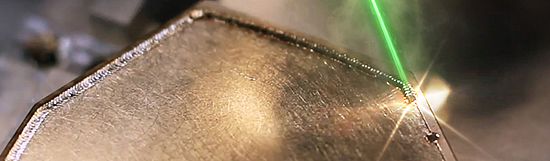
A critical stage in producing the lithium-ion batteries used in electric vehicles is seal-welding the top cap to the shell. Learn how the precision of direct drive technology allows laser welders to perform this micron-scale task significantly faster while improving control accuracy by 30% and achieving a yield rate over 99%.
Motion Control Fundamentals for Humanoids & Exoskeletons
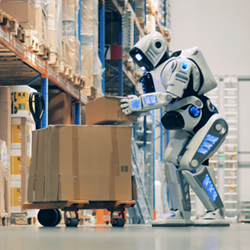
Tuesday, November 14, 2023, 11:00 a.m. ET
Design and build better humanoid robots and exoskeletons. Learn how to choose motion systems with the power, precision and efficiency to improve upon human capabilities, and to cost-effectively take your design from prototype to commercial production.
Save My Seat
AKD2G Quick Setup
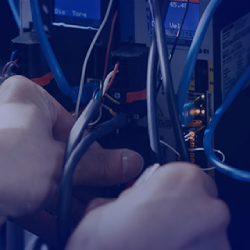
Wednesday, November 15, 2023, 11:00 a.m. ET
Learn how to use AKD2G Workbench software to set up your drive to perform next-generation motion tasks—quickly, confidently, productively.
Save My Seat
Advanced Configuration for AKD2G Dual-Axis
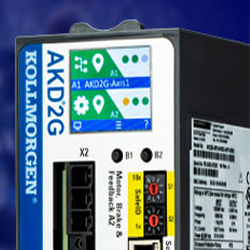
Thursday, November 16, 2023, 11:00 a.m. ET
Take full advantage of the dual-axis drive capabilities. Learn how to control two axes with one drive, including triggering inputs, tuning, troubleshooting and data capture.
Moog and Salvagnini: A Decentralized Control Architecture Adapted to Metalworking Applications
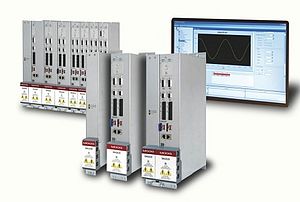
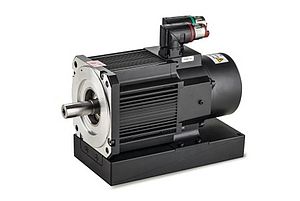
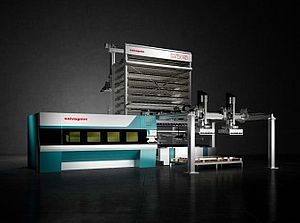
Moog Inc. (NYSE: MOG.A E MOG.B), a leading provider of high-performance drive technology solutions, and Salvagnini, also a leader in innovative solutions for the automation of metalworking applications, have jointly developed an 8-axis Cartesian handling robot for automatic guidance and sorting of punched or sheared parts designed and developed in machining centers.
Many metal processing companies face a variety of challenges, including high batch variability, smaller and diversified batches with special applications, and customer demands for shorter lead times and quality guarantees. Although the plant's systems and production lines are already designed to be flexible enough, current requirements often contradict this. Another option to meet customers' fast and diverse production needs is the Salvagnini 8-axis Cartesian manipulator. It fits into the existing concept of the room, fulfills various tasks and consumes less energy than comparable solutions on the market.
As Moog offers electric, hydraulic and hybrid solutions for machine development, Moog and Salvagnini were able to take a technology neutral approach. Moog engineers evaluated a range of technologies and selected the most appropriate solution for Salvagnini Cartesian Manipulator and Metalworking customers.
The Moog development team integrated its electromechanical solutions into the design of the Salvagnini robot so that the system is able to link different processes, including the transportation of the current workpiece from one station to another. To develop the multi-axis solution, Salvagnini engineers chose a DE2020 power control module, a DI2020 motor with integrated electronics, a DR2020 decentralized single-axis drive and HD/FAS H servo motors from Moog.
"In the arrangement of complex systems, it is difficult and not always possible to find space for a switchboard. "It is therefore very important to reduce the volume of the control box," explains Stefano Bizzotto, motion control manager at Salvagnini. “Ideally, the control box should disappear or be completely integrated into the floor plan of the machine. That's why we decided on decentralized drives and motors with integrated electronics."
By choosing electromechanical technology, we were able to design integrated plug-and-play systems that can communicate perfectly even with equipment from other manufacturers," adds Massimo Daziale, Moog's sales manager. “Simplified installation allowed for faster service. Other benefits include the smaller dimensions and lower weight of the machine's moving parts, resulting in greater acceleration and speed, as well as the ability to integrate new functions in the same space."
Together, Moog and Salvagnini upgrade existing machines to replace existing components or integrate new components. Modernizations are considered necessary because improving technological standards increases production efficiency while reducing operating costs. The intensive design and construction collaboration between the development teams of both companies is leading machine tool users to the next generation of increasingly connected systems focused on sustainability and Industry 4.0 readiness.
Moog is able to design the most appropriate combination of technologies and solutions to meet individual customer needs in these areas.
Optimize Form and Fit with Our 3D CAD Product Models
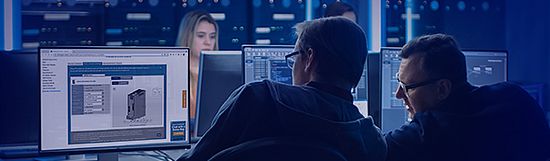
Search, configure and visualize more than 50,000 motion product models on demand. Then download 3D models in CAD for direct incorporation into your design.
Watch the Video
Direct Drive Helps Improve the Production Speed and Quality of Electric Vehicle Batteries
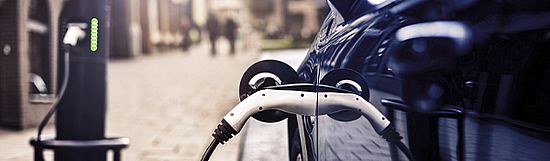
Blade batteries have become the most popular choice for electric vehicles due to higher safety performance, longer cruising range and faster charging speed. Learn how Kollmorgen helped a manufacturer of blade-battery production equipment significantly improve throughput and quality to meet the rapidly growing demand.
Minimize Weight and Size to Maximize Efficiency
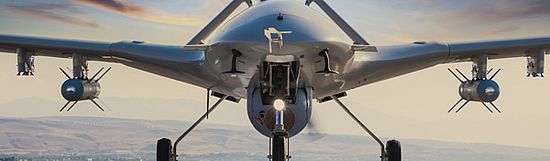
By specifying lighter, more compact, higher-efficiency motors, you can achieve optimum performance for positioning UAV flight-control surfaces, visualization systems, sensors, payloads and more. Learn how to design a more capable aircraft, bring it to market faster, and support it confidently throughout its lifecycle.
Correct Servo Motor Sizing for Continuously Holding Loads
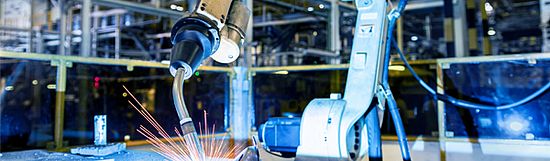
The word “stall” can mean very different things in different contexts. Be sure you’re applying it correctly when sizing AC servo motors that must continuously hold a load. Our white paper clarifies the technical issues and provides motor selection advice you can use, so you can be sure of safe, reliable operation.
Developing a High-Slice, High-Res CT Scanner: A Cross-Functional View
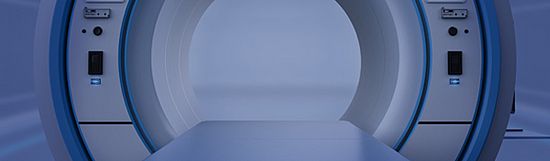
For any project involving high-performance motion, there are many stakeholders beyond the engineering team. Learn best practices for bringing together a successful cross-functional team focused on delivering innovative medical imaging machine designs.
Robot Ready: An Industry First
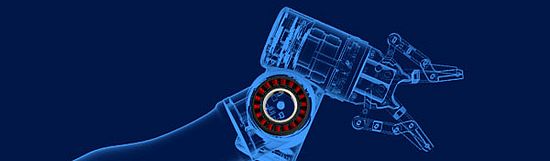
Get the highest torque density, at the speeds you require, in a robot-optimized form factor, with minimal temperature rise. TBM2G means no more tradeoffs.
Deliver High Performance in a Compact Form with TBM2G Frameless Motors
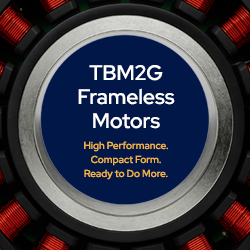
With significantly higher torque density in a more compact axial design, next-generation TBM2G frameless motors are ready to perform, ready to fit your design, and ready to scale. Learn how you can engineer a more capable machine, without compromise.
Get the Brochure
Get Higher Performance in Less Space with AKM2G Servo Motors
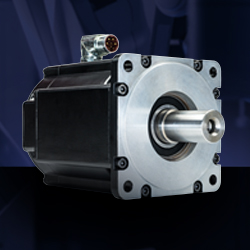
Next-generation AKM2G servo motors provide substantial performance improvement without changing the motor mounting or consuming more machine space. And they’re available with a wide range of options including extensive feedback, shaft, connector and support for functional safety.
Explore Now
Drive More Powerful Motion Solutions with AKD2G Servo Drive
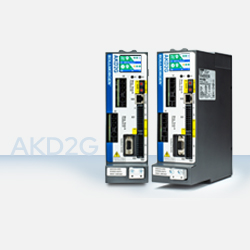
Integrated SafeMotionTM functions. Unparalleled connectivity. Higher power density. Simpler usability. Next-generation AKD2G drives put you in control to design more ambitious machines with more capable performance and more confident engineering. Learn more.
Get the Brochure
Accelerate Development, Increase Throughput and Maximize OEE with Kollmorgen Automation Suite™
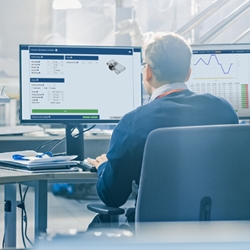
With controllers, drives, motors, communications and programming tools designed to work together, you can engineer more capable automation solutions. We put all the pieces together in one suite designed to make development of exceptional machines faster and easier.
Explore KAS
October Training Events
Register for the live session or to receive a link to the recording
Choose the Right Motor to Extend UAS Flight Time and Distance
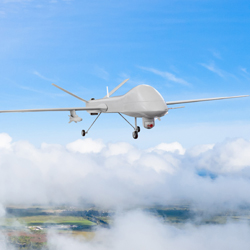
Wednesday, October 25, 2023, 11:00 a.m. ET
From saving lives to delivering goods, unmanned aerial systems help military, police, humanitarian and commercial organizations complete difficult missions efficiently and safely. Learn how to create motion systems optimized to help extend UAS flight time and range.
Save My Seat
The Gravity of the Situation: Vertical Load Handling for Automation
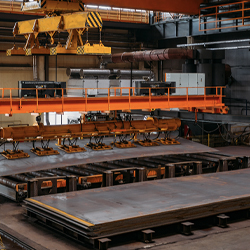
Thursday, October 26, 2023, 11:00 a.m. ET
When gravity is a factor in managing servo loads, you need to take special care in sizing the motion system, handling faults, ensuring employee safety and more. Join the experts as they walk you through best practices in a real-world application.
How to Set Up Your AKD for Success
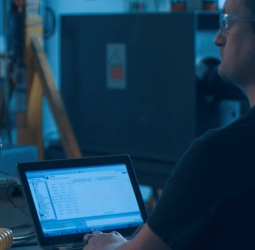
Wednesday, October 18, 2023, 11:00 a.m. ET
New to setting up a servo drive? Already experienced but looking for tips for a more effective setup process? This session is for you! Follow along and learn how to minimize setup time, apply best practices, and create precise motion—step by step.
Save My Seat
Advanced Motion with AKD
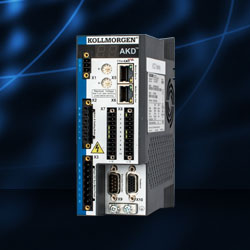
Thursday, October 19, 2023, 11:00 a.m. ET
Create intricate motion tasks, identify mechanical compliance, and increase performance by mastering the programming and diagnostic tools built into the AKD.
Clean Mirrors for Clean Energy
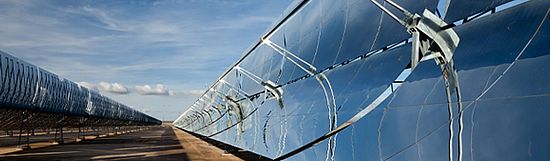
To keep energy flowing, heliostat solar plants need to keep thousands of massive mirrors clean. Learn how Kollmorgen motion helps increase maintenance efficiency by 500% and cleaning efficiency by 2,400% while operating in unpredictable terrain at temperatures often below –30ºC.
Learn how evolving principles of inertia matching affect your machine design
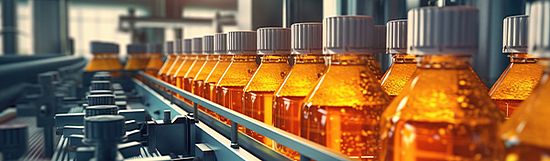
The old principles of inertia matching between load and motor are changing. Control algorithms are more advanced and processors are faster than ever. Whether you’re updating an existing machine or starting from scratch, get the best performance possible with help from Kollmorgen’s team of engineers. This whitepaper can get you started.
See Exactly How Your Motor Will Perform
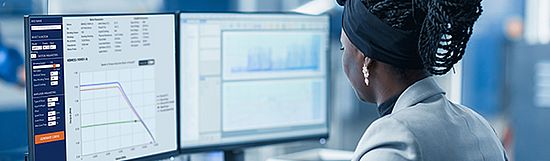
With just a few clicks, our Performance Curve Generator graphs the continuous torque, peak torque at different temperatures, and torque/speed characteristics of all our housed motors. There’s never been an easier way to evaluate the optimum motor for your application environment.
The New P80360 Stepper Drive
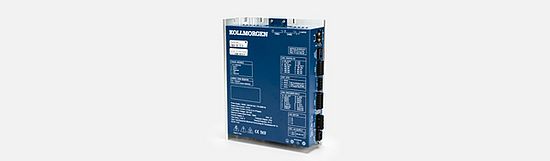
The feature-rich P80360 stepper drive offers closed-loop positioning, full programmability using an intuitive GUI, and faster setup with Kollmorgen motors. It’s ideal for point-to-point movements as well as linked motion sequences in a wide range of applications. Learn all the benefits and specifications.
Get the Features, Benefits and Specs of Kollmorgen’s Newest Drive

Now you can achieve near servo-like smoothness and precision with minimal risk of undershoot or overshoot even in compliant applications or when moving heavy loads. Get all the benefits and technical details of the fully programmable P80360 stepper drive with closed-loop position control.
Discover the Power of Kollmorgen Automation Suite™
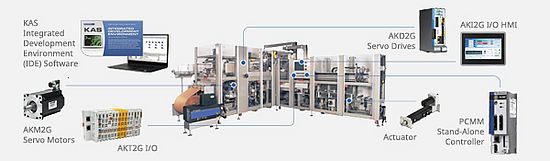
From complete manufacturing lines to small, automated desktop machines, the Kollmorgen Automation Suite (KAS) delivers a small yet powerful and cost-effective hardware platform ideally suited for modular or stand-alone machines that want the maximum in flexibility and performance.
From the Factory to the Farm: Washdown Servo Motor Technology
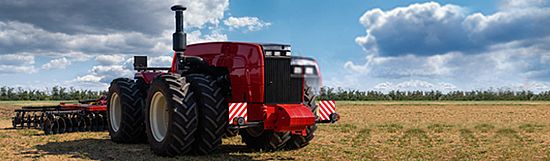
A new era of agricultural innovation is at hand. The same high-performance, washdown-capable motors used in food, beverage and pharmaceutical production promise to transform the productivity and profitability of farming automation. Learn why.
How Can You Design a More Capable Surgical Robot?
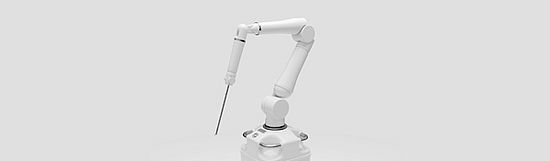
Surgeons value the ability to place instruments as closely together as possible when performing minimally invasive procedures. Learn how to design axially compact, high-torque robotic arm joints that help surgeons deliver better outcomes.
Providing You Engineering Expertise
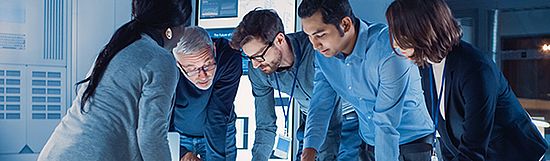
With decades of engineering experience in motion systems, we have a great base of knowledge to share. From white papers to blogs and free training, we are continually updating our content to keep you informed. Featured below is some of our most popular content.
Essentials of Motion Control
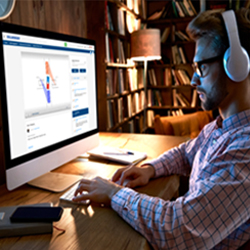
Register now and Learn at your convenience
The Essentials of Motion Control self-paced class, allows you to follow the path from electrical energy to physical motion, focusing on every opportunity to optimize motor efficiency and performance. Ready to get moving?
Get Started Now
Stepper Motor or Servo Motor: What are the key factors to consider?
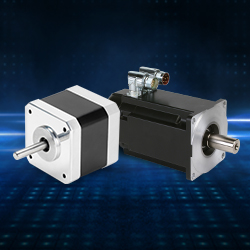
Stepper or servo? It’s one of the most common and important questions in motion engineering. And that’s why we’ve provided answers you can use in one of our most popular white papers ever. Read it, and make the right choice with confidence.
Get the White Paper
Three Design Considerations that Indicate a Machine Needs a Frameless Motor
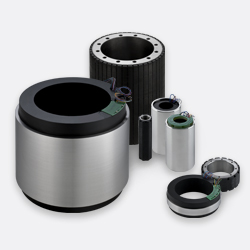
Does your machine need to operate in a smaller footprint, deliver enhanced performance or endure extreme conditions? Learn why a frameless direct-drive motor is likely your best solution.
Read the Blog
Still Designing to Decades-Old Inertia Matching Rules?
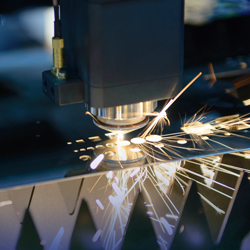
Machine Designers have pursued the idealized 1:1 inertia matching for the motor and load. But what if this rule no longer applied and you could use a significantly smaller motor and still achieve perfect motion? You can, and here’s how.
Get the White Paper
High Performance Machine Control Made Easy with Kollmorgen Automation Suite
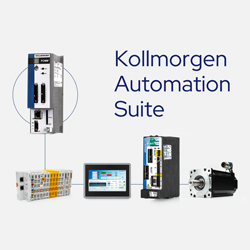
Tuesday, September 12, 2023, 11:00 a.m. ET
Kollmorgen Automation Suite delivers what you need to develop high-performance motion axes and bring your machine to market faster. Learn how to use the programmable motion controller and integrated development environment in this informative online training session.
Save My Seat
The Foundations of Electric Motion Motion 101 Online
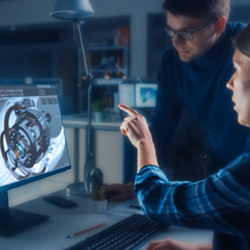
Wednesday, September 20, 2023, 11:00 a.m. ET
In this online training session, we’ll explore the foundations of electric motion and motor performance, including motor types, open versus closed loop control, how to configure optimum motion for each axis, and more.
Save My Seat
The Foundations of Motor Performance Motion 101 Online
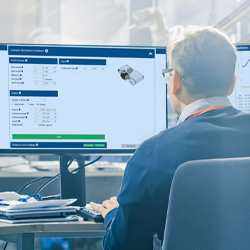
Thursday, September 21, 2023, 11:00 a.m. ET
Join this session to gain the practical knowledge you need to optimize servo performance, including how to specify the right feedback device and resolution, achieve efficient and cost-effective inertia matching, and more.
Save My Seat
Learn the Capabilities of Kollmorgen’s Advanced AKD Servo Drives
Kollmorgen's AKD servo drive is a flexible workhorse, with a wide range of models offering up to 48 A of continuous duty. Industry-leading bus options give you the freedom to use AKD servo drives in your preferred architecture and with a variety of proven Kollmorgen motors to drive innovation and increase the productivity of your machines.
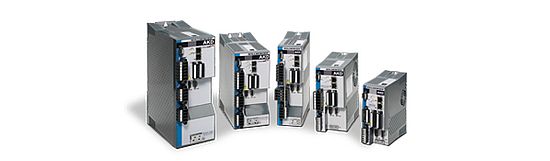
Direct Drive Technology Enhances Accuracy and Throughput for EV Battery Production
To meet the goal of 99% yield in lithium-ion battery production, manufacturers must achieve electrode coating with a thickness accuracy of plus/minus 1 micron. And they must do it while maximizing production throughput. Learn how Kollmorgen's advanced direct drive technology is making the difference for quality, productivity, profitability and a cleaner world.
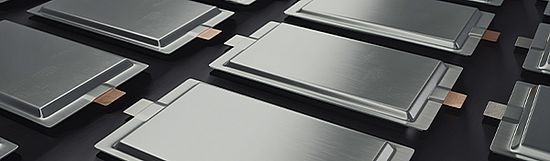
8 Tips to Reduce or Eliminate EMI Noise
Electromagnetic interference can wreak havoc with sensitive electronics, compromising the safety and reliability of your machine. Avoid unplanned downtime, loss of productivity or even hazardous operating conditions by implementing these 8 simple yet essential techniques.
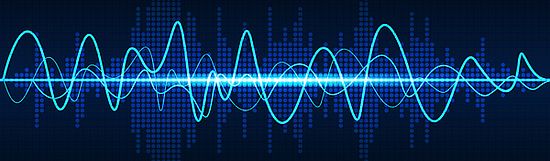
The Hazardous Location Certifications You Need
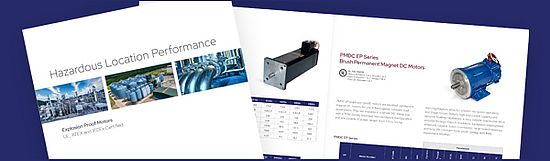
Finding motors that meet your performance specifications — and certified for hazardous-location use in your region — can be a challenge. Discover Kollmorgen’s wide range of UL, ATEX and IECEx certified motor technologies.
Improve Robot Efficiency Through Motor Design and Selection
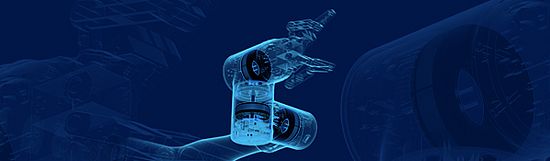
Robotic joints have unique performance requirements that impact how you select the correct motor. How can you minimize joint size while maximizing output power? What does efficiency mean for robotic applications? What about thermal constraints? Get expert answers to these questions and more.
Meet the Motion Challenges of LEO Satellites
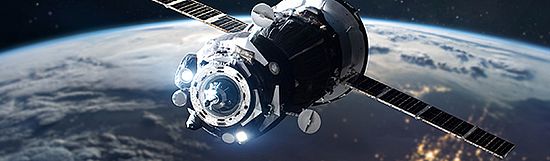
Tens of thousands of new satellites will be launched into low-Earth orbit (LEO) in the coming years. They will require compact motors that perform reliably in the extreme environment of space. With six decades of experience in space, Kollmorgen meets these demands on time and on budget.
Meet Kollmorgen’s New AKD2G 24A Servo Drive
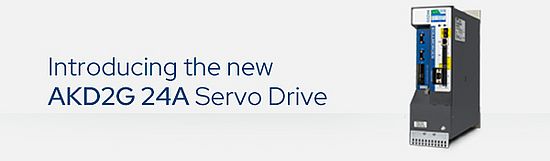
The new high-amperage AKD2G 24A servo drive brings higher levels of power, control and integration flexibility to Kollmorgen’s flagship servo drive line. Learn how this new drive simplifies integration in complex applications and delivers 3x the continuous current for satellite ground stations, robotics, packaging/labeling and more.
The Higher Amperage AKD2G 24A Servo Drive
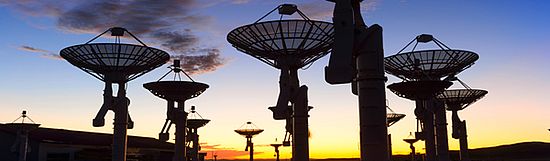
Satellite ground stations, robotics, packaging/labeling and other highly complex applications with high peak demands call for a drive that can handle extreme challenges. Learn how Kollmorgen’s new AKD2G 24A servo drive meets the need with 3x the continuous current and a rich feature set for simple, flexible integration.
5 Motion Tips for Optimal Metal Cutting Performance
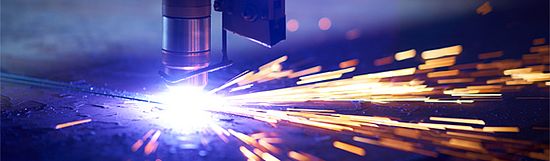
Whether you’re designing a new machine or upgrading an existing machine, next-generation performance depends on achieving the most precise and efficient motion possible. But where do you start? Read this guide to get tips to put your machine a cut above the rest.
Kollmorgen Motion for Mammography
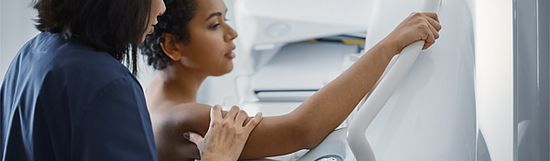
Advanced motion can make the difference for a mammography machine that adapts ideally to each patient’s anatomy, performs quicker scans, and minimizes unwanted movement to produce the clearest images. Learn how to build an imaging system that doctors and patients prefer.
Three Design Considerations that Indicate a Machine Needs a Frameless Motor
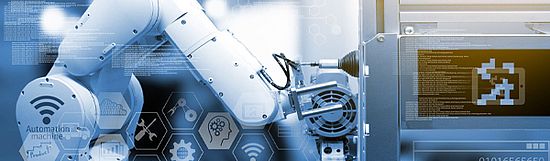
Does your machine need to operate in a smaller footprint, deliver enhanced performance or endure extreme conditions? Learn why a frameless direct-drive motor is likely your best solution.
Discover Compact Motors with Big Performance
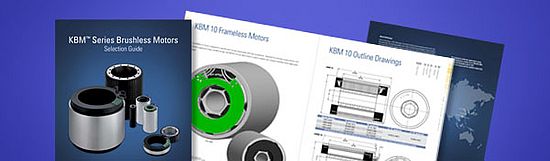
Frameless motors allow you to design a lighter, more compact machine with the precision of direct drive. Directly embedded in your machine’s own housing, they’re ideal for reliable performance in the most rigorous environments. Explore the possibilities.
Size Your Motor and Drive in Minutes
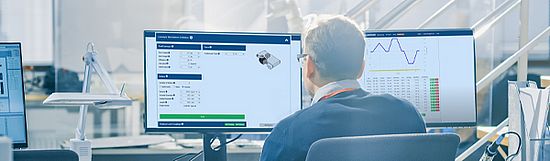
Keep it simple. If you know your application requirements, the Motioneering tool will guide you to the motor and drive pairings that best fit your needs.
Tips for Sizing and Programming Motion Control for Gantry Applications

Wednesday, August 16, 2023, 11:00 a.m. ET
Because you need to synchronize motion across multiple axes, designing and implementing a gantry application can be especially challenging. Learn the special considerations, product sizing methods and motion programming techniques that ensure success.
Save My Seat
Motioneering:

Sizing Your Application
Wednesday, August 23, 2023, 11:00 a.m. ET
If you’ve ever struggled to choose products with the best fit and performance for your application—or if you’ve never sized an application before—this session is for you. We’ll take you step-by-step through the process using the industry’s simplest, most powerful sizing tool.
Save My Seat
Motioneering: Creating Advanced Motion Profiles

Sizing Your Application
Thursday, August 24, 2023, 11:00 a.m. ET
Take a deep dive into the application-sizing capabilities of our online Motioneering tool. Learn how to create and edit the complex motion profiles that come into play when working with conveyor systems, electric cylinders, changing loads and more. Simplify a better design with Motioneering.
Save My Seat
AKD2G: The Advanced Servo Drive
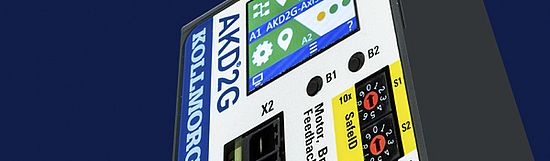
With embedded safety capabilities, a space-saving dual-axis design, single-cable technology and more, you can engineer a more compact, capable and reliable machine that’s easier to build and maintain. Learn all you can achieve with the AKD2G drive.
Conventional Motor or Slotless?
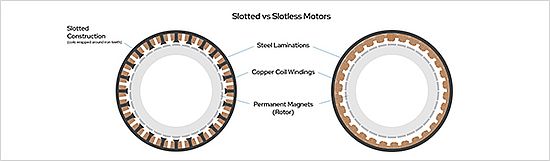
What's the best way to achieve high torque and smooth operation at relatively low speeds, as required for EO/IR applications? Let's cut through the misinformation and see what really matters in the choice between conventional versus slotless motors.
How Automation Adds Safety & Efficiency to Finishing Operations
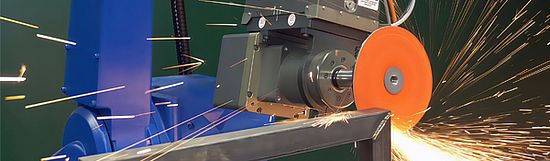
Safeguarding the welfare of operators in dangerous blending and finishing operations starts with automation. Learn how frameless servomotors enable end-of-arm robotic tooling to deliver a human touch while ensuring a safer manufacturing environment.
What are the different types of servo loops?
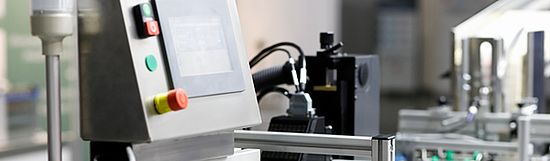
What does it mean to close them, and how is that accomplished? What difference does a closed-loop system make to the performance of your axis? Get answers you can use in this brief overview.
Reimagine Cobot Performance
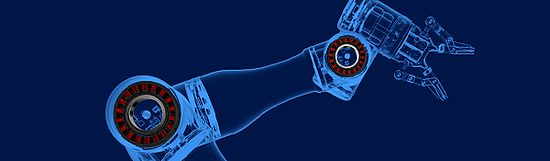
Your collaborative robot can be faster, stronger, more compact, more resilient. And you can bring it to market faster, with assurance of consistent frameless motor quality and supply, anywhere in the world. Learn how to engineer exceptional cobot capabilities with Kollmorgen as your partner.
Ask the Experts: Extreme Temperatures
Ambient and operating temperatures can significantly impact motor performance and longevity. Learn how to analyze and mitigate the effects of extreme temperatures in this on-demand webinar.
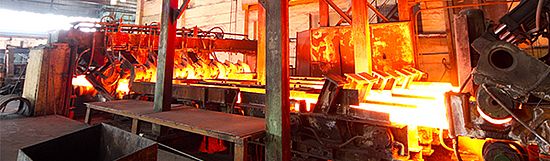
Enabling New Surgical Possibilities
High-torque, low-temperature, compact-size motors are the key to a game-changing surgical robot design. Learn how advanced motion is improving patient outcomes and quality of life.
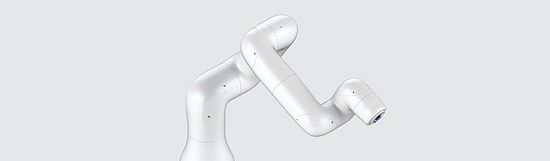
Bringing Performance and Reliability to Harsh Environments with Lightweight AKMA Motors
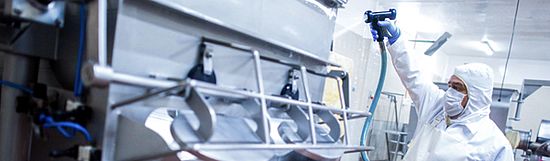
Are you ready to learn more about the AKMA motor and how it can deliver results for your application? Please join us while we cover topics such as Total Cost of Ownership, the new design features, and what applications this motor is best suited for.
Harsh Conditions. Limited Space. Now You Have the Right Motor.
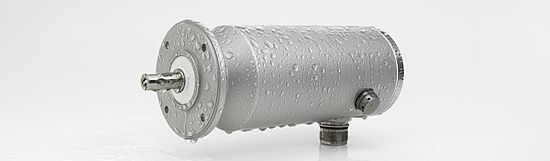
Looking for a lightweight motor for harsh environments? Our AKMA motor is built to perform, featuring a cost-effective anodized aluminum coating and versatile form factor for your demanding applications. Learn more about this workhorse motor.
The Right Motor For Tough Conditions

Whether you’re designing for tough medium or heavy washdown applications or all-weather conditions, AKMA motors offer the ideal feature set. See which AKMA motor meets your unique specifications with our streamlined product brochure.
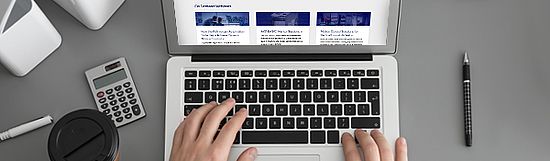
May Training Events Register for the live session or to receive a link to the recording

AKD2G Quick Setup
Wednesday, May 17, 2023, 11:00 a.m. ET
Learn how to use AKD2G Workbench software to set up your drive to perform next-generation motion tasks—quickly, confidently, productively.
Save My Seat
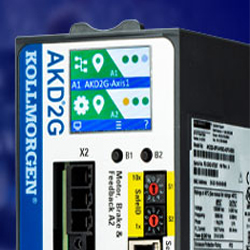
Advanced Configuration for AKD2G Dual-Axis
Thursday, May 18, 2023, 11:00 a.m. ET
Take full advantage of the dual-axis drive capabilities. Learn how to control two axes with one drive, including triggering inputs, tuning, troubleshooting and data capture.
Save My Seat
The Key to Next-Generation Surgical Robots
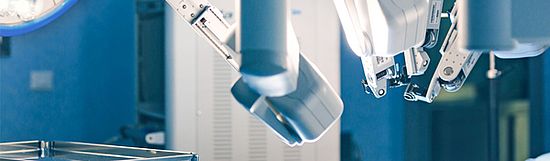
Surgeons want robotic cameras and instruments to operate as closely together as possible for an accurate field of view and minimal patient trauma. Learn how next-generation frameless motors are advancing the state of the art for high-performance, high-precision robots.
Stepper Motor or Servo Motor: What are the key factors to consider?
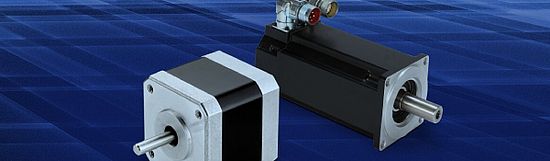
Stepper or servo? It’s one of the most common and important questions in motion engineering. And that’s why we’ve provided answers you can use in one of our most popular white papers ever. Read it, and make the right choice with confidence.
April Training Events
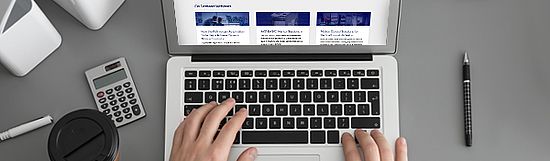
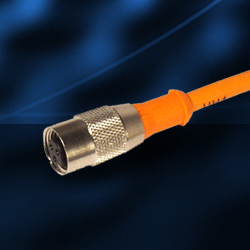
Preventing Electromagnetic Interference in Servo Cables
Wednesday, April 19, 2023, 11:00 a.m. ET
Power cables can cause electromagnetic interference that corrupts the position and velocity signals carried by nearby feedback cables. Learn how to tame EMI and ensure predictable servo motion.
Save My Seat
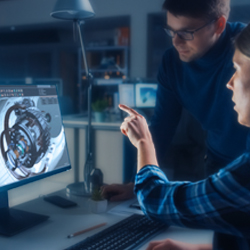
The Foundations of Electric Motion: Motion 101 Online
Wednesday, April 26, 2023, 11:00 a.m. ET
Learn the details of different motor types, open vs. closed loop control systems, and how to configure the optimum motion system for each machine axis.
Save My Seat
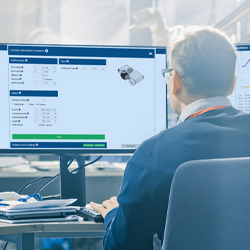
The Foundations of Motor Performance: Motion 101 Online
Thursday, April 27, 2023, 11 a.m. ET
Meet your motion performance goals with confidence. This course offers new insights into a wide range of topics, including the role of feedback type, feedback resolution and the influence of inertia.
Save My Seat
What’s the ideal motor for your robotic joints?
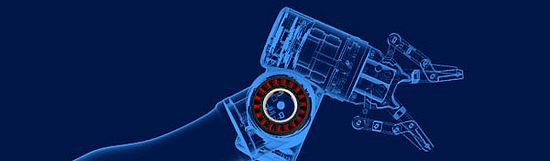
The No-Compromise Motor: TBM2G
Get the highest torque density, at the speeds you require, in a robot-optimized form factor, with minimal temperature rise. TBM2G means no more tradeoffs.

The Right Partner Can Drive Your Defense Program’s Success
Engineers are facing many challenges to keep up with their ever-evolving Aerospace and Defense requirements. How can you be more innovative and ambitious in your motion design, engineering, and delivery, while mitigating risk caused by supply chain and government regulations?
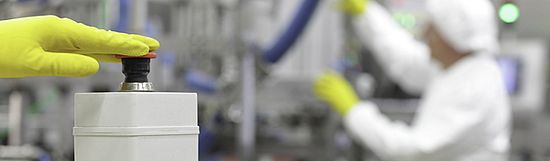
Differentiating Braking Techniques for Your Servo System
Wednesday, March 29, 2023, 11:00 a.m. ET
Proper servo motor braking is essential for employee safety while maintaining production requirements. But how do you choose which braking technique is right for your application? This session explores the applications for failsafe, dynamic and safe dynamic braking.
March Training Events
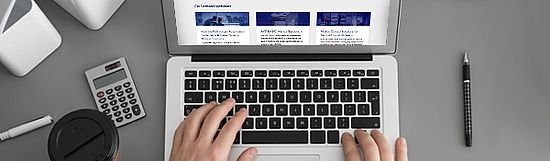
Register for the live session or to receive a link to the recording
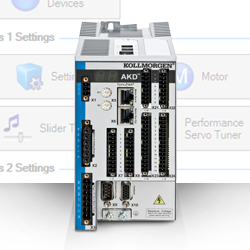
Step by Step Programming for AKD BASIC
Self-paced course
Are you looking to get the most out of your AKD BASIC drive? Learn how to program motion commands and create complex motion loops and interrupts in this self-paced online course.
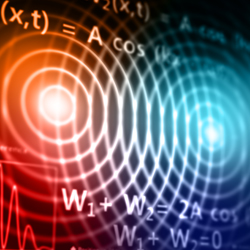
Grounding, Shielding and Bonding to Reduce Electromagnetic Interference
Thursday, March 9, 2023, 11:00 a.m. ET
Mitigating electromagnetic interference (EMI) is essential for sustaining precise motion, with no surprises. Learn why shielded cables are important, how to properly bond your cables to ground, and how to verify that the ground connection is functioning properly.
Save My Seat
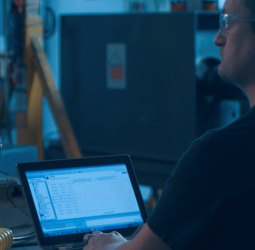
How to Set Up Your AKD for Success
Wednesday, March 22, 2022, 11:00 a.m. ET
New to setting up a servo drive? Already experienced but looking for tips for a more effective setup process? This session is for you! Follow along and learn how to minimize setup time, apply best practices, and create precise motion—step by step.
Save My Seat
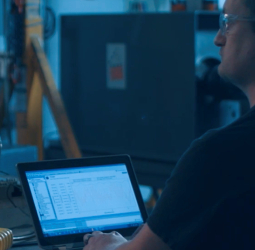
Advanced Motion with AKD
Thursday, March 23, 2023, 11:00 a.m. ET
Create intricate motion tasks, identify mechanical compliance, and increase performance by mastering the programming and diagnostic tools built into the AKD.
Save My Seat
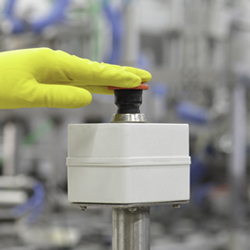
Differentiating Braking Techniques for Your Servo System
Wednesday, March 29, 2023, 11:00 a.m. ET
Proper servo motor braking is essential for employee safety while maintaining production requirements. But how do you choose which braking technique is right for your application? This session explores the applications for failsafe, dynamic and safe dynamic braking.
MOOG linear motors
Available in a variety of configurations, Moog linear motors provide dynamic and precise linear motion positioning for robotics, manufacturing automation, processing, packaging, test and simulation, and other industrial applications.
L3S and L3SK linear motors
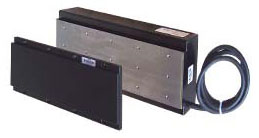
Moog's low-profile L3S air-cooled and liquid-cooled L3SK linear motors are designed for highly dynamic applications. L3S and L3SK motors are three-phase synchronous iron-core linear motors supplied as active parts (built-in motors). The laminates and the three-phase winding placed in their grooves form a ferromagnetic bundle, which in turn forms the primary part. This primary element is excited by permanent magnets in the secondary space, placed in a standard, static field and used as a magnetic path.
Both the L3S series engines and its liquid-cooled L3SK variant offer some of the widest power ranges in the industry. Standard models provide continuous force ratings ranging from 150 to 7,500 N for the L3S series and 300 to 12,000 N for the L3SK series when water is used as coolant. In addition, the air-cooled L3S series can be loaded with significantly higher forces and currents than those generated at nominal speeds. In comparison, the liquid-cooled L3SK series has almost twice the power and output of its air-cooled counterpart (L3S) with the same dimensions. Another advantage of the L3SK series is that they can work at higher ambient temperatures.
The modular design of two lines of linear motors supports a large number of options. In addition, Moog can offer fully customized solutions including:
- Winding and special insulation variants for systems designed for...
- various force constants (from approx. 40 to 1000 N/A)
- different intermediate circuit voltages (140 V, 330 V, 560 V, 700 V DC)
- Increased IP classes
- the air-cooled linear motor with an increased IP class is the L7S model
- the liquid-cooled counterpart is the L7SK.
- The position of the output cables can be changed*
Characteristics:
- Designed for highly dynamic applications
- High Force Overload Capability (L3S)
- High values of continuous force (L3SK)
- Quality production
- High assembly accuracy
- Long service life and high operational reliability
Advantages:
- High positioning accuracy
- Highly customizable
- High power density
- Various packaging options are available
LNS Linearmotoren
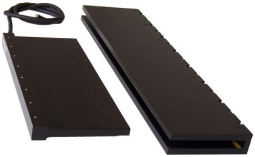
Moog LNS series ironless flat linear motors are designed for highly dynamic applications. The LNS series features synchronous linear motors that are supplied in the form of active parts (built-in motors). Due to the use of non-ferromagnetic material, the primary part of the motor is suitably light and highly efficient, with essentially no drag force (no gearing) and no pulsation of attractive forces.
Moog LNS motors provide sustained rated forces ranging from 16 to 225 N. In terms of electromagnetism, the LNS series is designed for an overload capacity of approximately five times the rated force. Thanks to this, they can be loaded with significantly higher forces and currents than those generated at nominal speeds.
The modular design of the LNS iron-free flat linear motor supports a large number of options. In addition, Moog can offer fully customized solutions. We offer customer-specific winding systems designed for different power constants (from approx. 10 to 100 N/A), as well as winding systems and insulation variants for different intermediate circuit voltages (140 V, 330 V, 560 V DC).
Characteristics:
- No gearing
- Designed for highly dynamic applications
- High power overload capability
- Reduced weight
- Quality production
Advantages:
- Flat design and compact dimensions
- High positioning accuracy
- Compensation of attractive forces
- Various packaging options are available
Better Motion Through Motioneering

How to use Motioneering to Size Your Application
Wednesday, February 22, 2023, 11:00 a.m. ET
Register to attend the live session or get a link to the recording
Learn how to use this powerful, online tool to size your system by specifying mechanism types, product selection criteria and more. You can even use Motioneering during the live session to size an application alongside the instructor.
Creating Advanced Motion Profiles
Thursday, February 23, 2023, 11:00 a.m. ET
Register to attend the live session or get a link to the recording
Size products and create complex motion profiles for additional mechanism types, such as conveyor systems and electric cylinders. This session will teach you best practices you can apply to any motion project.
Solve EO/IR challenges for land, air or space
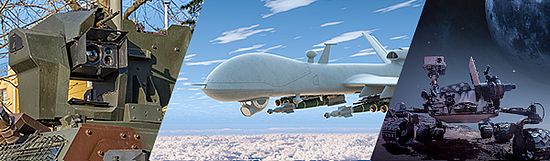
Holding a steady target despite the vibration and shocks of a moving land vehicle. Meeting the size, weight and power requirements of an aircraft. Enduring the G-forces, temperatures and radiation of space. Every electro-optical/infrared system poses specific motion engineering challenges. Learn how to solve them.
P8000 Series Stepper Drives
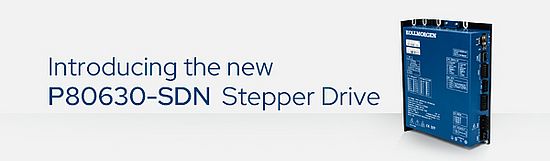
The Ideal Drive to Power Your Kollmorgen Stepper Motor
Our new P8000 series stepper drives take performance and precision to the next level. The first model, P80630-SDN, offers superior accuracy in a more compact design for labelers, indexing, CNC, packaging, pumps and other applications requiring low-speed, point-to-point motion control for fixed loads. And there are more of these advanced drives soon to come.
Stepper or Servo Motor?
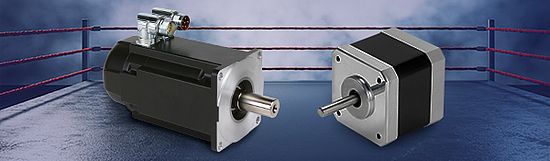
Here’s how to decide
Stepper and servo systems each have advantages based on their differing design and operating principles. Understanding these differences is the key to choosing the best technology for your application. Check out our Blog in Motion for an overview of the most common selection scenarios.
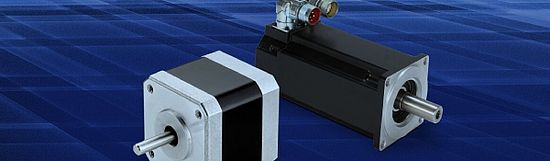
Want a deeper dive?
Supercharge your motion expertise with our new guide, “Stepper Motor or Servo Motor: Which Should It Be?” We’ll walk you through detailed considerations of torque and speed, inertia matching, coordination of axes, accuracy, resolution and more. There’s even a handy decision table to make your choice easy.
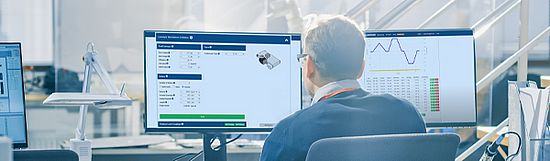
Size Your Motor and Drive in Minutes
Keep it simple. If you know your application requirements, the Motioneering tool will guide you to the motor and drive pairings that best fit your needs.
Fast, Precise, Reliable Motion
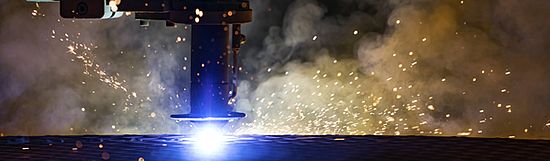
Optimize the performance of your high-definition metal cutting machine
Whether you’re designing a new or upgrading an existing machine, next-generation performance depends on achieving the most precise and efficient motion possible. From your fieldbus architecture to your feedback devices and more, these optimization tips can put your machine a cut above the rest.
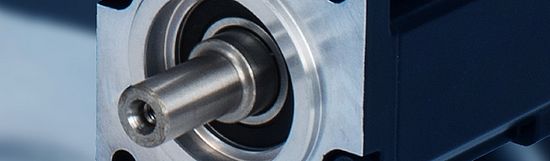
Discover all there is to know about how servo motors work
Learn the history of servo motors, key elements in their design, and how feedback devices and controls complete the system. You’ll also learn the types of control loops from the simplest examples to multiple embedded current, velocity and position loops hat enable servo efficiency and precision.
AKD2G Servo Drives
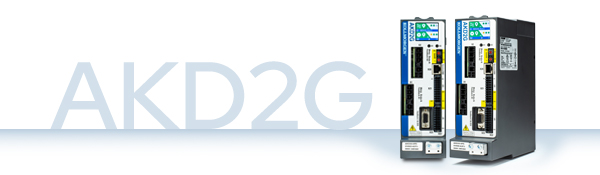
Give Your Machine the Power to Be More
Integrated SafeMotion functionsTM. Unparalleled connectivity. Higher power density. Simpler usability. Next-generation AKD2G drives put you in control to design more ambitious machines with more capable performance and more confident engineering. Learn more.
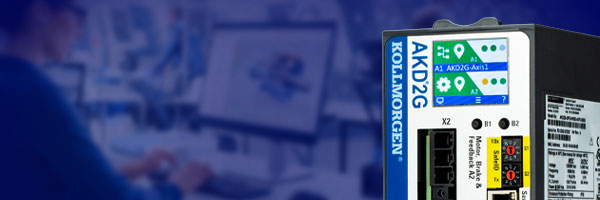
5 Key Reasons to Consider an Upgrade to AKD2G Servo Drives
AKD drives will continue to deliver great performance for many years to come. But whether you’re upgrading an existing machine or designing a new one, the next-generation AKD2G drive offers several key advancements. How much value could they add to your machine?
Compact, Precise, Powerful
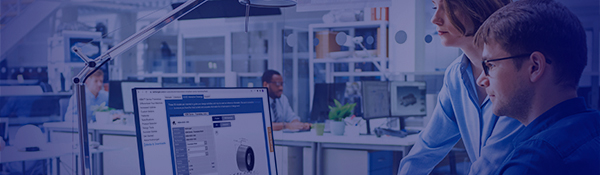
Optimize Frameless Motor Performance
All it takes is five steps or less to optimize a frameless motor for your application. In most cases, an off-the-shelf motor or a cost-effective standard modification will provide the exact fit and performance you need—with no custom development required. Learn how easy it can be.
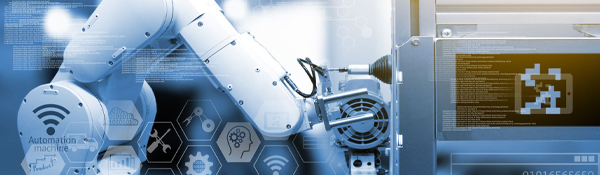
Three Design Considerations that Indicate a Machine Needs a Frameless Motor
Does your machine need to operate in a smaller footprint, deliver enhanced performance or endure extreme conditions? Learn why a frameless direct-drive motor is likely your
best solution.
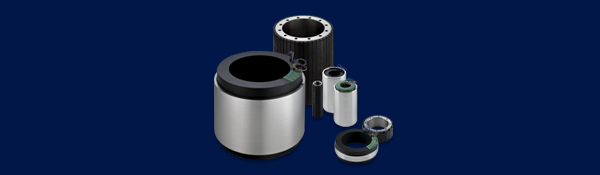
Discover KBM Series Frameless Motors
Eliminate the bulk and mechanical compliance issues of transmission components while providing exceptional protection from rigorous environments. It’s all possible with KBM.
Reimagine Cobot Performance
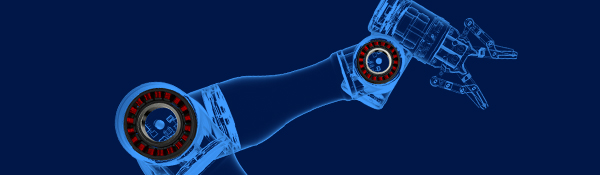
Robot-Ready Motors Create New Possibilities
Your collaborative robot can be faster, stronger, more compact, more resilient. And you can bring it to market faster, with assurance of consistent frameless motor quality and supply, anywhere in the world. Learn how to engineer exceptional cobot capabilities with Kollmorgen as your partner.
Ready to Design. Ready to Perform. Ready to Scale.
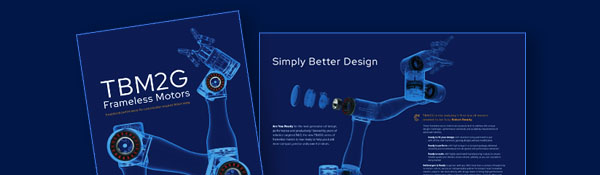
Take your cobot design to the next generation of performance and manufacturability. TBM2G motors pair with standard harmonic gearing, deliver the highest performance, and are always available in the sizes, specifications and options you need.
TBM2G frameless motors

The new TBM2G frameless motors provide torque density and next-generation speed in a more compact package. They are ready to adapt to your design, increase its performance and expand to full production. Smaller engines for big engineering ideas - are you ready?
TBM2G — Get all the details
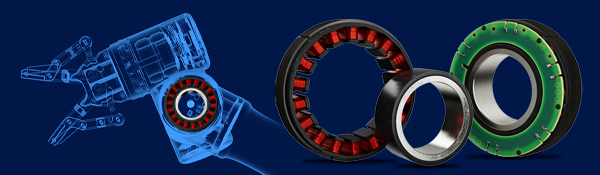
Reconsider the possibilities of a frameless motor. Learn the TBM2G series design philosophy, performance specifications, target applications and more
Choose your TBM2G
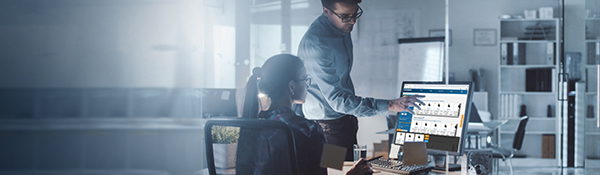
Our online product selection tool can help you get started on the road to finding the perfect engine. Start by clicking on Rotary Motors with direct drive.
Simplify Machine Design with Stepper Motors
If you’re looking for precise motion with easy setup, then stepper motors should be your first choice. They offer servo-like positioning without the need for complex feedback devices. See the benefits and how you can find the right motor for you.
Max Torque, Small Size
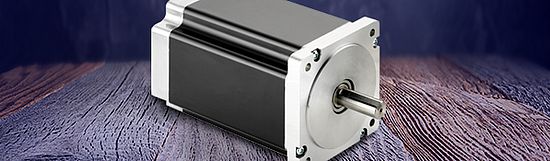
The CT Series of motors uses innovative cooling technologies and magnetic designs to deliver higher current and torque ratings at a lower temperature. CT stepper motors can support large mechanical loads without worry due to the oversized bearing design.
Modular I / O terminals for any requirements
The Koltmorgen AKT2G I / O terminals offer all the functions you need to connect digital and analog sensors and actuators, encoders, thermocouples, bus couplers and more to the EtherCAT® bus in real time. Adding these terminals to your system couldn't be easier with automatic recognition and automatic configuration.
Step in motion: The best applications for stepper motors

Do you need full servo control, or can a simple and economical stepper motor serve your application just as well? Watch this on-demand web session to learn how stepper motors work, their benefits, the best applications, and how to choose the best stepper motor for your needs.
Energy exploration and refining, mining, grain and textile mills, paint shops and more: Every dangerous place has very specialized requirements for movement. Get the engines you need, certified to global UL, ATEX, CSA and CCC standards and supported by service and support within a region, region.

When choosing an explosion-proof motor, you will first want to understand the different types of hazardous locations and engine construction techniques that ensure safe operation. Get a quick overview of our new blog post on the go.
Online, interactive, product selection form from KOLLMORGEN
Choose with confidence every time. Watch our instructional video!
Find out how easy Perfect-Fit movement can be From torque, speed and power to form factor, control Elements and accessories - perfect fit is the key to your success applications. With our selection tools, you can choose with confidence movement products. Our tutorial video will show you how simple it is can be. Check it!

How does a servomotor work?
Do you need a servomotor? AC or DC? Brushed or brushless? How can you precisely control its torque, speed and position? In this webinars we got answers to questions about your servo system. Watch and learn anytime, whenever it suits you!
Moog products ensure a successful Mars Rover landing

Moog Inc. (NYSE: MOG.A and MOG.B) today announced that the company's space products have played a critical role in NASA's successful Perseverance Rover landing on Mars. Perseverance is NASA's latest mission to explore Mars and builds on the success of the 2012 Mars Curiosity Rover mission. The Moog team designed, built and tested several components necessary for the mission. During the final descent, the Moog throttle assemblies controlled the inlet spacecraft's engines. The spacecraft entered the atmosphere at 12,500 miles per hour, stabilizing and lowering the level of the Perseverance Rover until it successfully touched Lake Crater at approximately 4:00 p.m. ET today.
Moog also played a key role in launching the Rover on the Red Planet. The mission fired from Cape Canaveral, Florida, on July 30, 2020. Moog propulsion took the launch vehicle out of Earth's atmosphere. In addition, Moog rocket engines were used to steer a 350 million-mile spacecraft carrying the Perseverance Rover, ensuring it stayed on course at 55,000 miles per hour. With Rover now safe on the Red Planet, Moog technology will continue to support the mission. Moog valves and filters will help keep the Rover drill clean when digging samples during one Mars, which is 687 days on Earth.
"I am proud of the work that our talented and dedicated team members have put into this project to ensure its success. Their ingenuity and commitment drive innovation and the continued success of Moog, our local community, and exploring worlds beyond our own, ”said Maureen Athoe, president of Moog’s Space and Defense. Steve Witkowski, market manager for space electronics, added: “From the engineers who create the individual hardware, to our technicians integrating the individual components into a larger system, it is truly a mission in a mission. It's unbelievable to think that your work is an important element in exploring another planet.
"Mars 2020 is another major step forward in space exploration and another significant success in Moog's Space and Defense," added Steve McDonald, manager of propulsion engineering. "Seeing how our hardware successfully fulfills such an important mission is both inspiring and fulfilling."