OPCom Phosphate Ester - particle monitor

ARGO-HYTOS offers the OPCom particle monitor – it is a compact device for continuous monitoring of the number of polluting particles in hydraulic and lubricating media.
Currently, the offer of these proven devices has been expanded to include the OPCom Phosphate Ester design.
OPCom Phosphate Ester – is a device intended for measuring the pollution of liquids based on phosphate esters.
LubCos H2O+II – oil condition monitoring
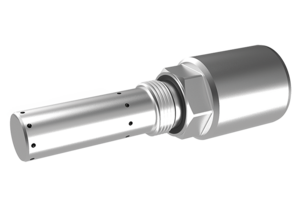
LubCos H2O+II extends the capabilities of the LubCos H2O oil relative humidity sensor to also monitor electrical conductivity and relative permittivity.
The LubCos H2O+II sensor continuously measures temperature, relative humidity, electrical conductivity and relative permittivity of hydraulic oil. By measuring and recording changes in these quantities, changes and aging of the hydraulic fluid can be detected. In this way, it is possible to prevent malfunctions in the hydraulic system caused by the quality of the hydraulic fluid. And it also helps in scheduling hydraulic fluid maintenance and determining when it needs to be replaced.
Technical parameters
- measured oils:
- mineral oils (H, HL, HLP, HLPD, HVLP)
- synthetic esters (HETG, HEPG, HEES, HEPR)
- polyalkylene glycols (PAG)
- zinc- and ash-free oils (ZAF)
- polyalphaolefins (PAOs)
- maximum working pressure 50 bar
- supply voltage 9...33 VDC
- protection IP 67
- relative humidity measurement range 0...100%
- relative permittivity 1...7
- electrical conductivity 100...800,000 pS/m
- temperature measurement range -20...85 °C
- output analog signal 4...20 mA
- communication interface RS232 / CANopen
- connection with M12x1 8-pin connector
LubCos H2O – oil relative humidity monitoring
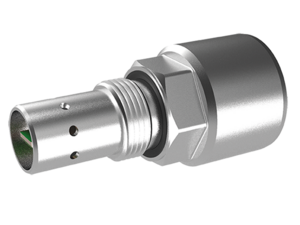
Water is undesirable in hydraulic and lubricating media. High concentrations of water can cause serious malfunctions in operation as well as damage to machines and equipment.
LubCos H2O measures the relative humidity of the oil directly and displays the percentage degree of water saturation of the oil:
0%: absolutely dry oil
100%: the oil is completely saturated with water - it is no longer able to absorb additional moisture and the water will already occur freely
When analyzed in the laboratory, oil moisture is evaluated as the absolute water content in ppm (Parts per Million).
The advantage of measuring relative humidity compared to absolute measurement of water content is that it is not necessary to know other parameters of the oil or its saturation limit to assess whether the water is free or bound.
Technical parameters
- measured oils:
- mineral oils (H, HL, HLP, HLPD, HVLP)
- synthetic esters (HETG, HEPG, HEES, HEPR)
- polyalkylene glycols (PAG)
- zinc- and ash-free oils (ZAF)
- polyalphaolefins (PAOs)
- maximum working pressure 50 bar
- working temperature range -40...105 °C
- supply voltage 9...33 VDC
- protection IP 67
- relative humidity measurement range 0...100%
- temperature measurement range -20...85 °C
- output analog signal 4...20 mA
- communication interface RS232
- connection with M12x1 8-pin connector
Monitoring of cleanliness and wear using modern particle counting technologies.
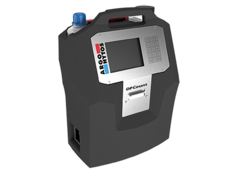
Hydraulic systems look at the hydraulic fluid as a system element that has to meet a variety of requirements - to transfer power, to lubricate, to drain away heat, to drain impurities from the system into the filter. There are many causes for a fault in the hydraulic system, apart from mechanical damage or overloading of individual components, the quality of the hydraulic fluid is also considered. Particularly solid particulates in hydraulic fluid are the main cause of wear and damage to individual components of the system. Unwanted particles can enter the system from the outside, but also form in the hydraulic system itself.
Consequences of contamination of the working fluid are increased wear, damage to individual parts of the system as well as reduced performance and shortening of service life. Pollution of hydraulic fluid causes increased costs for the operator of the plant. This is why it is necessary to use multiple types of filters in the hydraulic system to maintain the required purity of the working fluid. To further reduce costs, increased attention must be paid to detecting increased wear and thus preventing damage to the device at an early stage. Different sensors and particle number monitoring devices are available for this purpose. This makes it possible to provide an efficient and relatively low cost solution for almost every application.
Particle count measurement
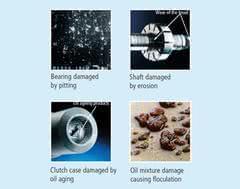
Automatic particle number sensors provide the best price-performance ratio, allowing real-time particle size and particle counting. Alternative techniques such as microscopy or gravimetry are complex, error prone, and inefficient compared to real-time measurements.
The benefits of real-time measurement compared to traditional laboratory analyzes are not only less labor and total costs, but mainly continuous on-line monitoring of working fluid status. The measured values give an overview of the total pollution of the working fluid as well as the time course of the pollution. Based on these measurements, a predictive maintenance system can be implemented.
Optical particle count
The standard for measuring real-time particle count is the optical method based on the principle of light blocking according to ISO 11500. This method is most widespread due to its reliability and low cost. In this method, the measured sample flows through the capillary (volume) in which the particles are counted. If there are no particulate matter in the volume, the light will irradiate the measured sample without the shadows and thus impact on the photodiode.
If particulate matter passes through the measured volume, there is a blocking of the light emitted. This causes shadows on the photodiode. The size of the shades is proportional to the particle size. The measured number of particles in relation to the volume is evaluated as the concentration of the pollutants. The device allows pollutant evaluation according to various standards (ISO 4406: 1999, SAE AS 4059, GOST 17216 and NAS 1638) that can be set on the device.
Particle calculator
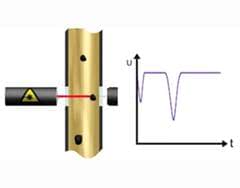
Particle compartments are particularly suited for extremely accurate measurement of contamination of working fluid in a laboratory or field. With OPCount, Argo-Hytos offers the latest-generation particulate computer that has been designed for use in hydraulic machines and equipment. The integrated measurement of the number of particles in the volume of volume ensures in connection with the first-class components that each particle flowing through the sensor is accurately measured.
The integrated pump allows real-time measurement into a measuring vessel or measurement with return of the measured sample back to the tank. The device can be intuitively operated via the touch screen. Measured data and other sample information (temperature, viscosity, oil type, etc.) can be stored in the device memory or printed out directly. The accessories needed for the measurement can be stored directly in the device, making it easier to handle this device. OPCount can also connect other Argo-Hytos sensors from the LubCos series, which are designed to monitor the state of the liquid. This allows you to track other parameters such as temperature, humidity and oil quality.
Particle number monitoring
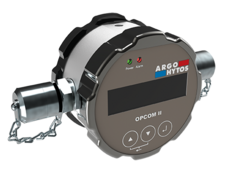
For systems where the particle number measurement is realized not only automatically but also permanently, it is necessary to permanently install a suitable device in the hydraulic system.
In this case, compact and durable devices are recommended, which can be easily integrated into the existing hydraulic system. Requirements for stationary or mobile measurements are high - among other things, resistance to high pressures, wide range of temperatures, dust, vibration, humidity. These requirements meet the Argo-Hytos OPCom Particle Computer.
The proven areas for installing OPCom for particle counting are oil purity tracing in heavy-duty industrial applications such as presses or injection molding machines for plastics.
Inductive particle count measurement
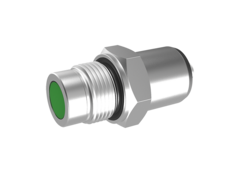
Ferromagnetic particle detection products (particle debris products) are suitable induction particle sensors. The ferromagnetic particle detector OPCom FerroS is specially designed for gears, which is an economically advantageous alternative to conventional monitoring of working fluid contamination.
OPEM FerroS wear sensor operates on the principle of a magnetic plug on which ferromagnetic particles accumulate as well as a permanent magnet. The coil in the sensor head detects accumulated particles and produces a measured signal that is proportional to the accumulated amount of pollutants. This sensor is easy to integrate into existing systems without requiring flow control of the working fluid, as is the case with other sensors designed to monitor pollution.
conclusion
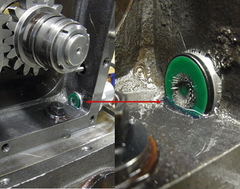
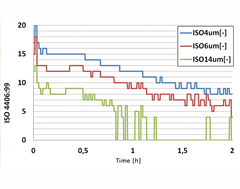
The use of advanced technologies to monitor the amount of pollutants in service fluids makes it possible to apply new concepts to service and maintain these oil fillings. This makes it possible to extend the oil fill interval, to identify the increased wear of the system elements and thus to prevent damage and also to predict the maintenance of the equipment.
Peter Lauko
Tel.: +421 37 7777 955
Mobile: +421 903 282 644
Fax: +421 37 7777 967
Email:lp@bibus.sk
Jaroslav Tvrdoň
Tel.: +421 37 7777 954
Mobile: +421 914 336 525
Fax: +421 37 7777 967
Email: tvr@bibus.sk
Vladimír Begáň
Tel.: +421 37 7777 954
Mobile: +421 914 336 527
Fax: +421 37 7777 967
Email:vbe@bibus.sk